par Sharon Thatcher
Transitioning to light-gauge steel construction is not a decision to be taken lightly, but Todd Tober, owner of Tober Building Company, Richfield, Ohio, is glad he did. His more traditional construction GC company was started eight years ago with two employees and is now one of five interrelated companies he owns employing 53 workers. Much of his growth can be attributed to incorporating LGS/CFS into his list of building options.
DÉBUT DE CARRIÈRE
Tober a commencé sa carrière dans la construction en tant que menuisier syndiqué. "Mon expérience est avec les poteaux métalliques traditionnels", a-t-il noté.
Il a ouvert sa propre société d'entreprise générale et de promotion immobilière en 2013, axée principalement sur le marché de l'habitation multifamiliale. "Nous allions bien, mais la question était toujours de savoir comment faire mieux", a-t-il déclaré.
Il a eu l'opportunité de rénover un bâtiment de construction modulaire qui a été achevé à l'origine en 1980. Il a aimé le concept et a décidé : « Trouvons un moyen de faire du modulaire nous-mêmes ».
Ils ont d'abord expérimenté le bois. « Nous avons commencé avec du bois et je n'aimais pas la qualité du produit que nous produisions. Le bois est du bois et il rétrécit, se déforme et se fissure, et il est incohérent, alors nous avons abandonné l'idée du bois et avons commencé à construire avec de l'acier », a-t-il déclaré.
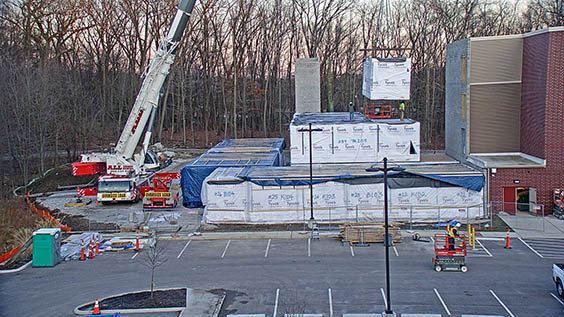
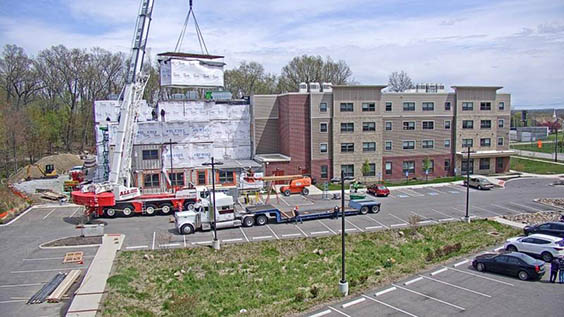
Unités modulaires ToVee mises en place par une grue. Ils étaient utilisés pour créer un ajout à un bâtiment existant.
LE VOYAGE VERS LGS/CFS COMMENCE
Rencontrer Tom Reed, le représentant américain de Howick Ltd., a changé la donne. Après des discussions et des nuits blanches, Tober a ensuite acheté deux machines Howick pour la construction de nouveaux immeubles d'appartements modulaires dans le cadre de son entreprise de développement. En utilisant le logiciel 3D standard, REVIT, son entreprise en croissance lente a pu intégrer des plans détaillés dans sa production. L'une des machines produit des goujons métalliques de 3.162 pouces allant de bobines de calibre 16 à 20; leur plus grand Howick 7800, le seul en Amérique du Nord, produit cinq profilés en goujons métalliques de 6, 8, 10, 12 et 14 pouces à partir d'une bobine de calibre 12-16.
"A partir du logiciel 3D, nous avons pu produire un fichier de machine CNC qui serait introduit dans la profileuse pour produire nos poteaux métalliques à installer dans les unités d'appartements modulaires", a-t-il décrit, ajoutant : "Ce sont des poteaux sur mesure, avec étiquetage où la piste et les goujons se rencontrent. Les connexions sont très faciles.
Mais les projets de développement de Tober ne sont pas consécutifs et laisser ses machines de profilage en sommeil ne semblait pas très efficace. "Ainsi, le directeur de l'usine et moi avons trouvé un moyen de générer des revenus dans l'usine alors que nous attendions le lancement du prochain projet modulaire", a déclaré Tober. L'idée était de fournir du matériel pour leurs projets d'entreprise générale.
Leur premier cas test était un projet de préservation historique à Canton, dans l'Ohio, transformant un bloc de 1910 et un bâtiment scolaire en béton en logements pour personnes âgées abordables. Le bâtiment, inactif depuis environ 20 ans, a été vidé pour faire table rase. La nouvelle entreprise dérivée de Tober, Atlas Framework, a été chargée de produire les montants métalliques. "Nous sommes sortis et avons disposé tous les murs de l'appartement dans le logiciel 3D", a-t-il décrit, puis nous avons envoyé ce que nous appelons des packs de production - juste des paquets de panneaux muraux - sur le chantier. Le logiciel était essentiel pour déterminer comment gérer les nombreuses variations de mesure du bâtiment vieillissant qui ont été créées au fil des années d'altération, d'usure et de tassement.
Au début de la construction du nouvel intérieur, le succès de la charpente LGS/CFS est rapidement devenu évident. "Ce que nous avons vu, c'est cette énorme économie de main-d'œuvre, car la production de ce type de charpente avec des poteaux personnalisés est beaucoup plus rapide que ce que vous avez généralement dans les charpentes métalliques traditionnelles", a déclaré Tober.
Contrairement aux charpentes métalliques traditionnelles qui sont coupées sur place, l'équipe de Tober a utilisé le système LGS/CFS pour prémesurer, prédécouper et prépercer pour le placement des boulons. Sur le chantier, les pièces étaient simplement boulonnées en place comme un ensemble de montage. La rapidité de la construction a atténué les inquiétudes concernant le prix du métal, l'une contrebalançant l'autre.
La formation d'une équipe de construction habituée à des techniques de construction plus traditionnelles n'était pas un problème majeur, mais cela a nécessité l'adhésion de l'équipe.
"Nous avons dû envoyer une nouvelle chose sur le chantier et espérer que l'équipe - habituée à faire les choses dans un sens - adopterait le nouveau processus", a déclaré Tober, "et littéralement en une heure, ils ont compris comment lire les dessins et comment assembler les choses. C'était une courbe d'apprentissage très rapide.
Il a analysé les chiffres et découvert que leur méthode de construction LGS/CFS est 400 % plus rapide que la charpente traditionnelle.
UNE ENTREPRISE, MAINTENANT CINQ
Today, Tober operates five businesses: Tober Building Company, his general contracting company that operates mainly in Northeast Ohio; Tober Development Co., the land development side of the business; ÀVee, a modular manufacturing company operating in Ohio, Pennsylvania, Indiana, and Michigan building complete units shipped to job sites; P&G Electric, a commercial electrical company; and Atlas Frameworks, producing framing packages that can be shipped anywhere. Atlas framing packages were being used for a hotel project in Canada at the time of this interview.

Photos avec l'aimable autorisation de ToVee
POINTS DE VUE SUR L'AVENIR DE LGS/CFS
Tober fait partie d'une poignée d'entrepreneurs à l'échelle nationale qui utilisent LGS/CFS, mais il estime que ce n'est qu'une question d'habitude qui empêche les autres de le rejoindre dans ce qu'il trouve un domaine lucratif.
« Il est difficile de convaincre les gens de changer », a-t-il déclaré. "Tout le monde dans le domaine de la construction sait qu'une fois que vous avez appris à gagner de l'argent avec une certaine méthode, vous hésitez à changer... Ils ont inventé la cloueuse à air comprimé et il a fallu un certain temps pour que les gens passent des marteaux aux cloueuses, mais vous savez, c'est une évidence, il faut juste du temps pour changer.
Il accorde beaucoup de crédit à ses employés pour avoir facilité le changement. L'année dernière, ils ont connu leur plus forte croissance avec l'ajout de 30 employés. Le personnel compte six modélisateurs BIM pour la conception du projet.
"Nous avons une équipe vraiment, vraiment géniale", a déclaré Tober. "Les gens font l'entreprise et je pense que nos employés sont les meilleurs dans notre entreprise. Ils ont rendu le processus plus fluide et ont facilité la transition d'une méthode de construction à celle-ci. »
Tober a également traversé les obstacles pour obtenir la certification ICC. « C'est l'organisme directeur de l'industrie de la charpente métallique, nous nous conformons donc à toutes leurs spécifications. Nous suivons un processus d'assurance qualité très strict pour nous assurer que chaque pièce d'acier que nous envoyons est conforme aux normes que nous avons définies dans notre processus de certification.
Tober a déclaré qu'il utilisait toujours du bois, mais qu'il trouvait de plus en plus de moyens d'intégrer LGS/CFS. "Je pense que le défi est de comprendre ce qui fonctionne et ce qui ne fonctionne pas", a-t-il déclaré, ajoutant : "Le nom du jeu est d'être créatif et flexible et c'est ce que nous essayons de faire." RF
ARTICLES LIÉS
La popularité de LGS/CFS devrait augmenter