di Sharon Thatcher
Il passaggio alla costruzione in acciaio di scartamento leggero non è una decisione da prendere alla leggera, ma Todd Tober, proprietario della Tober Building Company, Richfield, Ohio, è contento di averlo fatto. La sua più tradizionale società di costruzioni GC è stata fondata otto anni fa con due dipendenti ed è ora una delle cinque società interconnesse di sua proprietà che impiega 53 dipendenti. Gran parte della sua crescita può essere attribuita all'incorporazione di LGS/CFS nella sua lista di opzioni di costruzione.
PRIMA CARRIERA
Tober ha iniziato la sua carriera nel settore edile come falegname sindacale. "Il mio background è con le tradizionali borchie di metallo", ha osservato.
Nel 2013 ha aperto la sua società di general contracting e sviluppo immobiliare, focalizzata principalmente sul mercato degli alloggi multifamiliari. "Stavamo andando bene, ma la domanda era sempre: come possiamo fare meglio", ha detto.
Ha avuto l'opportunità di rinnovare un edificio modulare che è stato originariamente completato nel 1980. Gli è piaciuto il concetto e ha deciso: "troviamo un modo per fare da soli".
Per prima cosa hanno sperimentato con il legno. “Abbiamo iniziato con il legno e semplicemente non mi piaceva la qualità del prodotto che stavamo producendo. Il legno è legno e si restringe, si deforma e si incrina, ed è incoerente, quindi abbiamo scartato l'idea del legno e abbiamo iniziato a costruire con l'acciaio”, ha detto.
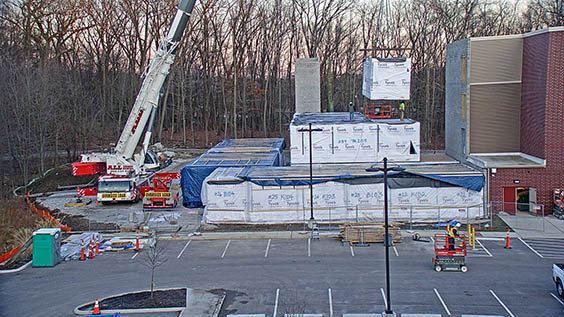
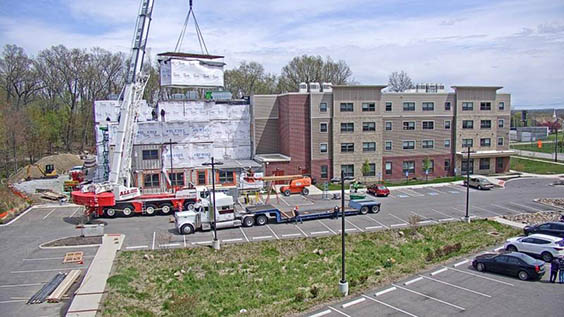
Le unità modulari ToVee vengono posizionate con la gru. Sono stati utilizzati per creare un'aggiunta a un edificio esistente.
INIZIA IL VIAGGIO VERSO LGS/CFS
L'incontro con Tom Reed, il rappresentante di vendita negli Stati Uniti di Howick Ltd., è stato un punto di svolta. Dopo discussioni e notti insonni, Tober ha successivamente acquistato due macchine Howick per la costruzione di nuovi condomini modulari nell'ambito della sua attività di sviluppo. Utilizzando il software 3D standard, REVIT, la sua azienda in lenta crescita è stata in grado di incorporare piani dettagliati nella loro produzione. Una delle macchine produce perni in metallo da 3.162 pollici che vanno da 16 a 20 calibri; il loro Howick 7800 più grande, l'unico in Nord America, produce cinque profili in perni metallici da 6, 8, 10, 12 e 14 pollici da bobina calibro 12-16.
"Dal software 3D siamo stati in grado di produrre un file macchina CNC che sarebbe stato inserito nella rulliera per produrre i nostri prigionieri di metallo da installare nelle unità modulari dell'appartamento", ha descritto, aggiungendo: "Questi sono prigionieri personalizzati, con etichettatura dove si incontrano la pista e le borchie. I collegamenti sono molto facili.”
Ma i progetti di sviluppo di Tober non sono back-to-back e lasciare inattive le sue macchine di profilatura non sembrava molto efficiente. "Quindi, il direttore dell'impianto e io abbiamo trovato un modo per generare entrate in fabbrica mentre stavamo aspettando l'inizio del prossimo progetto modulare", ha detto Tober. L'idea era di fornire materiale per i loro progetti di appalti generali.
Il loro primo banco di prova è stato un progetto di conservazione storica a Canton, Ohio, che ha trasformato un edificio scolastico in cemento armato del 1910 in alloggi per anziani a prezzi accessibili. L'edificio, inattivo per circa 20 anni, è stato sventrato per creare tabula rasa. La nuova società spin-off di Tober, Atlas Framework, è stata incaricata di produrre le borchie di metallo. "Siamo usciti e abbiamo disposto tutte le pareti dell'appartamento nel software 3D", ha descritto, e quindi abbiamo inviato quelli che chiamiamo pacchetti di produzione, solo fasci di pannelli a parete, al cantiere". Il software è stato essenziale per determinare come affrontare le numerose variazioni di misurazione dell'edificio invecchiato che sono state create in anni di agenti atmosferici, usura e assestamento.
Quando è iniziata la costruzione dei nuovi interni, il successo dell'intelaiatura LGS/CFS è diventato subito evidente. "Quello che abbiamo visto è stato questo enorme risparmio di manodopera perché la produzione di questo tipo di intelaiatura con borchie personalizzate è molto più veloce di quella che si ha in genere nelle tradizionali intelaiature con borchie in metallo", ha affermato Tober.
A differenza delle tradizionali strutture metalliche tagliate in loco, il team di Tober ha utilizzato il sistema LGS/CFS per premisurare, pretagliare e preforare per il posizionamento dei bulloni. Sul posto di lavoro, i pezzi sono stati semplicemente imbullonati in posizione come un set di erettori. La velocità di costruzione ha alleviato le preoccupazioni sul prezzo del metallo, con uno che controbilancia l'altro.
L'addestramento di una squadra di costruzione abituata a tecniche di costruzione più tradizionali non è stato un grosso problema, ma ha richiesto il consenso della squadra.
"Dovevamo inviare una nuova cosa al cantiere e sperare che la squadra, abituata a fare le cose in un modo, avrebbe abbracciato il nuovo processo", ha detto Tober, "e letteralmente nel giro di un'ora hanno capito come leggere i disegni e come mettere insieme le cose. È stata una curva di apprendimento molto veloce e veloce”.
Ha sgranocchiato i numeri e ha scoperto che il loro metodo di costruzione LGS/CFS è il 400% più veloce dell'inquadratura tradizionale.
UN BUSINESS, ORA CINQUE
Oggi Tober gestisce cinque attività: Tober Building Company, la sua società di appalti generali che opera principalmente nel nord-est dell'Ohio; Tober Development Co., la parte aziendale dedicata allo sviluppo del territorio; To Vee, un'azienda di produzione modulare che opera in Ohio, Pennsylvania, Indiana e Michigan costruendo unità complete spedite ai cantieri; P&G Electric, un'azienda elettrica commerciale; e Atlas Frameworks, producendo pacchetti di cornici che possono essere spediti ovunque. Al momento di questa intervista, i pacchetti di cornici Atlas venivano utilizzati per un progetto alberghiero in Canada.

Foto per gentile concessione di ToVee
OPINIONI SUL FUTURO DELLA LGS/CFS
Tober fa parte di una manciata di appaltatori a livello nazionale che utilizzano LGS/CFS, ma ritiene che sia solo una questione di abitudine che impedisce ad altri di unirsi a lui in quello che trova un campo redditizio.
"È difficile convincere le persone a cambiare", ha detto. "Chiunque nel campo delle costruzioni sa che una volta che impari a fare soldi con un certo metodo sei riluttante a cambiare... Hanno inventato la pistola sparachiodi ad aria e ci è voluto un po' prima che le persone cambiassero dai martelli alle pistole sparachiodi, ma sai, è un gioco da ragazzi, ci vuole solo tempo per cambiare.
Dà molto credito ai suoi dipendenti per aver reso il cambiamento più facile. L'anno scorso hanno visto la loro crescita più grande con l'aggiunta di 30 dipendenti. Sul personale ci sono sei modellatori BIM per la progettazione del progetto.
"Abbiamo una squadra davvero fantastica", ha detto Tober. “Le persone fanno il business e penso che il nostro personale sia il migliore nel nostro business. Hanno reso il processo più fluido e hanno semplificato il passaggio da un metodo di costruzione a questo”.
Tober ha anche superato gli ostacoli per ottenere la certificazione ICC. “Questo è l'organo di governo dell'industria delle strutture metalliche, quindi rispettiamo tutte le loro specifiche. Passiamo attraverso un processo di garanzia della qualità molto rigido per assicurarci che ogni pezzo di acciaio che inviamo soddisfi gli standard che abbiamo stabilito nel nostro processo di certificazione".
Tober ha detto che usa ancora il legno ma sta trovando sempre più modi per incorporare LGS/CFS. "Penso che la sfida sia capire cosa funziona e cosa no", ha detto, aggiungendo: "Il nome del gioco è essere creativi ed essere flessibili ed è quello che stiamo cercando di fare". RF
ARTICOLI CORRELATI
La popolarità di LGS/CFS dovrebbe crescere