作者:Jaswinder Bhatti,Samco Machinery
滚压成型曾经以非常慢的速度运行,大约每分钟 50 英尺。 然后很容易在行尾手动处理所有事情。 如今,轧辊成型机可以以每分钟 300 到 500 英尺的速度运行。 速度会使零件难以处理,但零件配置也会如此,随着机器功能的扩展,零件配置变得更加复杂。
通常,零件是滚压成型的,然后在生产线上手动合并附加功能和流程。 当今的滚压成型系统可能包括一些与滚压成型本身无关的冲压、成型、弯曲和其他工艺,它们是为完整的一体式零件制造而设计的。 这些系统伴随着复杂的材料处理自动化。
从一个过程转移到另一个过程,自动化材料处理消除了人为错误,尤其是与零件方向有关的错误。 自动化有助于验证是否正在处理正确的零件,并对其进行定向以进行正确的处理。 同样的一个例子是在暖通空调行业,在滚压成型后,零件被送到装配线,空调直接组装在上面。
它还有助于减少对操作员的依赖,从而增加滚压成型的正常运行时间和速度。 物料搬运系统的处理速度比任何操作员都快得多,尤其是当生产线上的零件又大又重时。 大而重的部件带来了安全方面的问题。 全天手动必须反复移动和定位零件会使操作员感到疲劳和受伤。
使用自动化材料处理系统可以节省大量时间,尤其是在包装和嵌套方面。 操作员有时可能会丢失零件运行的计数,并且可能会因订单不准确而发货。 计算零件运行以确保正确完成订单的能力可以节省时间,无论是在前端有库存,还是有信心知道订单不需要复制和重新发货。 操作员不需要在整个制造过程中不断地进行计数。
COVID-19 还展示了自动化物料搬运系统的其他好处。 制造商必须遵守严格的协议,以限制工作空间中的人数并保持适当的距离。 这些系统减少了操作辊压成型设备和维持安全标准所需的工人数量。
你需要知道什么
对于拥有现有滚压成型机的制造商来说,了解为什么以及如何需要材料处理自动化非常重要。 大多数商店的车间空间有限,合并这些系统可能会占用比当前分配的空间更多的空间,这意味着可能需要对设备进行重组。 这需要仔细规划,尤其是在涉及二级流程的情况下。
一些商店可能看不到添加这样一个系统的初始价值,尤其是前期成本。 但机器不会休息,并将全天以相同的处理速度继续运行。 通过消除人为因素并保持工艺的一致性,制造商可以期待显着的吞吐量提升,有时甚至高达 35%。
尽管人们普遍对自动化材料处理系统感兴趣,但并非所有制造商都需要这种系统。 调查一家商店是否可以从新设备中受益非常重要,尤其是因为在许多情况下前期成本很高,以及现有和未来制造活动的最佳选择是什么。 是否有足够的容量用于自动化物料处理? 如果是这样,流程中的瓶颈在哪里?在哪里可以最好地使用自动化?
前端系统
有许多辊压成型领域的自动化可以带来好处,并且应该基于客户要求和机器规格。
线圈处理。 根据需要,有许多不同的线圈处理系统可供选择。 您需要多久更换一次线圈? 这需要完成的速度是多少? 有几个选项可用于自动线圈处理。
使用材料时,可以使用单端或双端开卷机来更换线圈。 单一选项往往速度较慢,但不会在车间占用太多空间。 双头开卷机,一侧运行,可以装载第二侧线圈,以最大限度地减少停机时间。
带卷车和翻卷机组合允许在开卷机仍在运行时将线圈装载到带卷车上,这在车间的其他部分使用起重机时会很有帮助,因为可以将心轴预加载到车上. 线圈车可以与单开卷机或双开卷机配对以提高效率。 通常线圈是直视天空的。 然后操作员必须使用起重机将线圈提升到垂直位置。 这个过程可能非常危险,因为线圈有可能打滑。 但翻转者将安全地将线圈带到直立/垂直位置。 另一方面,翻转器/线圈车组合还可以通过将部分使用的线圈从垂直位置带回眼睛到天空的位置来安全卸载部分使用的线圈以被带走。
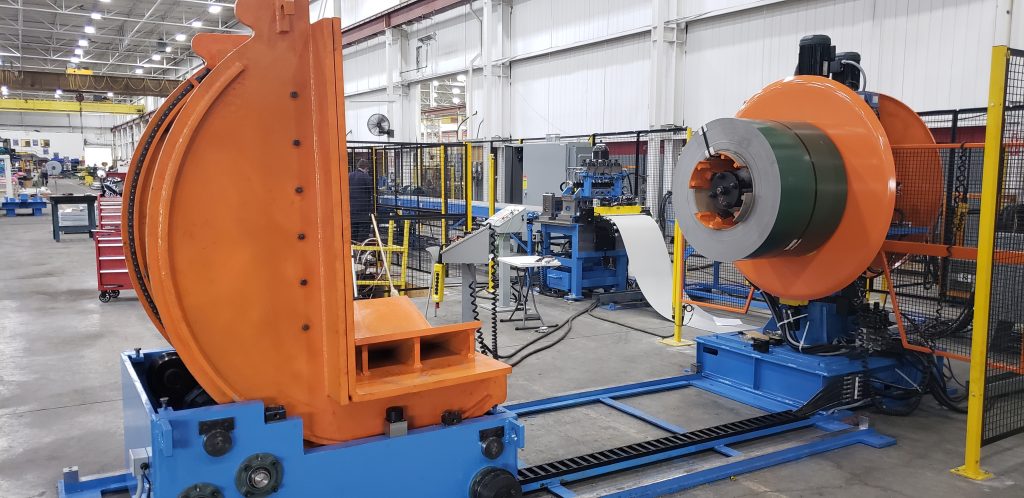
带卷车和翻卷机组合允许在开卷机仍在运行时将线圈装载到带卷车上,
累加器。 从开卷机上出来的卷材进入蓄能器,然后被送入轧辊成型机。 当整个线圈都在蓄能器中时,可以在不停止滚压成型过程的情况下更换线圈。 更换线圈后,材料会再次进入蓄能器。 这种自动化每次更换线圈最多可以节省 10-15 分钟。
端剪焊机。 这允许操作员连接正在运行的线圈的后缘和新线圈的前缘,以节省将线圈送入整条生产线的时间。 它可以节省停机时间并限制手动进料造成的损坏(减少废品)。
拾取和放置系统。 它不是一次手动进料一个坯料,而是在动力输送机上拾取和放置预切材料。 它可以适当地选择右手和左手部分。 拾取和放置系统可用于正确定位零件以进行弯曲或冲压等后处理。
后端系统
滚压成型过程完成后,制造商如何处理零件? 有多种自动化材料处理选项可用于在辊压成型线末端集成以提高效率。
巢穴。 这用于成品以高线速下线。 它收集并嵌套一组或成捆的成品,通常用于螺柱和轨道行业,以进行包装和运输。 Nesters 消除了在滚压成型线末端对多个工人的需求。
堆垛机。 该材料处理系统将成品零件堆叠在滚压成型线的末端,并通过编程以每个堆叠的预定数量的零件将堆叠移动到叉车拾取的区域。
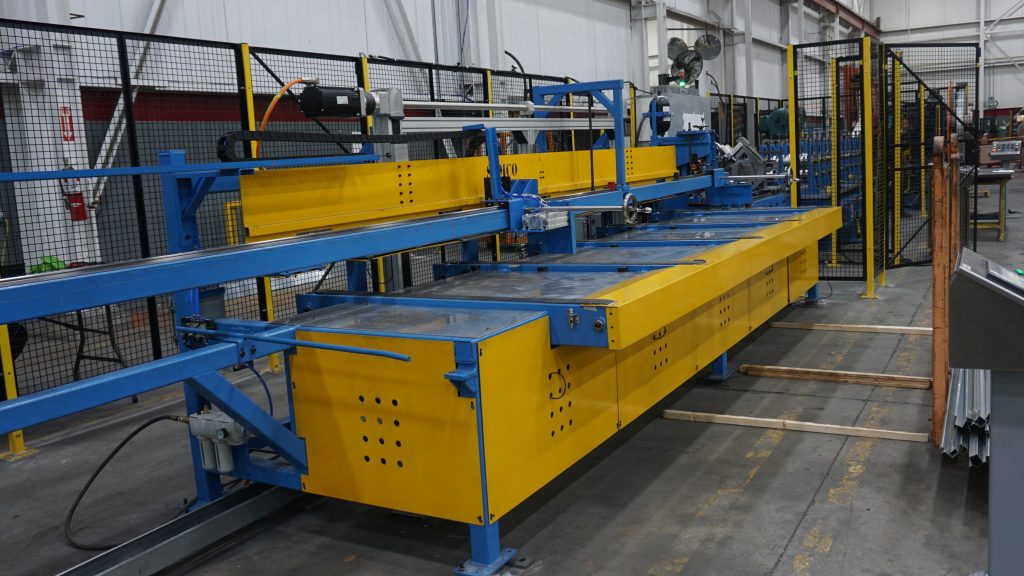
嵌套机消除了在滚压成型线末端对多个工人的需求。
打包机。 零件从辊式成型机上脱落后,它们被嵌套成迷你束。 捆绑器自动处理迷你捆绑包并自动构建预编程的主捆绑包,这些捆绑包可以根据零件订单和批次进行运输。 主捆升降台上升以接收来自机器的第一层产品,并随着堆叠的增加而下降。 然后将它们捆绑成一个单元进行运输。 一旦该主捆完成,升降台会一直下降并将完成的捆送至最终出口端辊道输送机。 该物料搬运系统无需手动提升包装捆,并减少因提升和转动重型成组部件而造成的伤害。
打包。 一旦零件从辊式成型机上取下并捆绑或堆叠,就需要进行适当的包装,以确保零件安全到达而没有损坏。 包装系统可以包括收缩包装,在每个部件之间添加塑料或纸片,添加垫料和捆扎带,或用气泡包裹包裹,以便将其装载到卡车上。
下一波创新浪潮
随着许多不同的自动化材料处理系统到位,拥有一个监控系统很重要。 今天的机器速度如此之快,以至于操作员无法跟上零件的加工速度,这使得确保零件正确生产变得更加困难。
在流程中添加质量检查或监控是我们将在我们的滚压成型系统中看到的越来越多的事情。 自动化材料处理系统能够识别所有零件、识别不良零件并在捆绑和运输之前将它们分离出来,这将节省大量成本和时间。
最新最好的自动化材料处理系统可以使任何制造商的生活更轻松。 通过滚压成型工艺手动处理零件所需的员工更少,消除了安全问题,并让工人腾出时间进行其他工艺。 即使添加其中一两个选项,也可以使滚压成型过程更快、更可靠。 并非每个商店都需要顶级设备,但重要的是要了解现有和未来的需求,这样您才能适应设备。 定制滚压成型生产线应基于滚压成型机及其能力、零件生产需求以及对前期成本和投资回报的了解。 射频
贾斯温德·巴蒂 是应用工程副总裁 三科机械, 安大略省多伦多市; www.samco-machinery.com。