Considere sus opciones antes del reemplazo
¿Cómo sabe cuándo es el momento de reemplazar sus herramientas de rodillos? Es una pregunta común planteada por los operadores de perfiladoras. Según Ben Schmidt, gerente de ventas de la industria de The Bradbury Co., una mirada de cerca al producto final ayuda a responder esa pregunta.
“Normalmente, la forma en que diagnosticamos un problema de herramientas es observando lo que tenemos saliendo del extremo del formador de rollos”, dijo, enfocándose en el panel agrícola estándar de calibre 26 a 29, 36″ de ancho con ¾ costillas.
El borde de superposición ondulado, un efecto de arco cruzado, paneles más anchos, características reducidas del panel (como costillas mayores y menores redondeadas versus afiladas) y una baja calidad posterior al corte son signos probables de que hay problemas con las herramientas. Hay momentos en que esas degradaciones requieren el reemplazo inmediato de herramientas y otros momentos en que una acción intermedia puede extender la vida útil de su máquina.
“Básicamente, existen dos tipos diferentes de desgaste de herramientas”, explicó, “un evento catastrófico… y el desgaste normal”.

Con un evento catastrófico, “algo malo pasó; puedes verlo cuando sucede”.
También puede verlo en forma de daños en la pintura del panel. Probablemente comenzó como un mal ajuste que hizo que las herramientas se unieran, acero contra acero, lo que resultó en marcas en la pintura y acumulación de pintura en las herramientas.
La doble lámina es otro signo visible de un evento catastrófico, cuando más de una lámina de acero intenta atravesar su máquina al mismo tiempo. “Cuando sus herramientas están diseñadas para un máximo de calibre 26, 0.020 (20 milésimas de pulgada), y envía tres hojas de 015, ahora tiene material de 0.045″ tratando de atravesar un espacio de 0.020″. En el peor de los casos, su máquina se detiene, en el mejor de los casos [el panel] atraviesa el molino, pero termina con algunas áreas desgastadas [en su herramienta] que eliminarán inmediatamente sus radios de curvatura”, dijo Schmidt.
Cuando ocurre un evento catastrófico, lo más probable es que sea necesario reemplazar las herramientas.
Con el desgaste normal, debería notar una disminución gradual en el radio de curvatura de sus herramientas. “A medida que trabaja con acero, los radios de curvatura disminuirán, se aflojará, puede verlo en los troqueles”, dijo Schmidt. Los técnicos usan calibres de radio para verificar el desgaste.
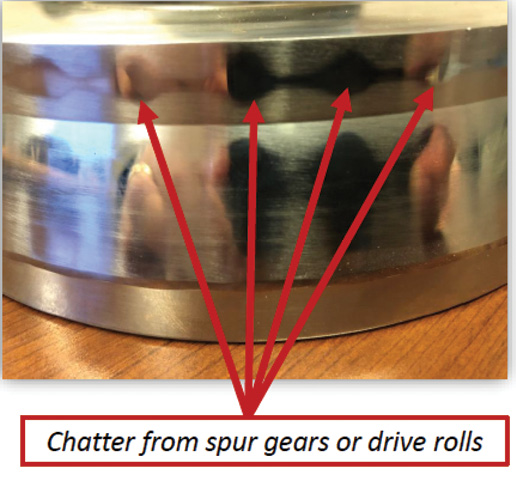
El desgaste normal también puede afectar la línea de transmisión y crear lo que se llama "vibración" en el panel, que es un efecto de remolino. La vibración también puede ser causada por la holgura de la cadena. “El eje inferior de la formadora de rodillos es una parte fija, generalmente es lo que se acciona, y cuando acciona la parte superior, normalmente con un engranaje recto, si los engranajes se desgastan o la línea de transmisión se desgasta, se afloja”, dijo.
La holgura afecta la forma en que el material se alimenta a través de la máquina y afecta las matrices de su máquina.
“Lo que verá en el panel cuando tenga parloteo, cuando mire hacia abajo en su costilla menor, verá marcas de remolinos que bajan a través de él”.
Schmidt señaló que la única forma de deshacerse de la vibración es recortar o reemplazar las herramientas.
Comprender y manejar el desgaste normal ayudará a evitar problemas de calidad a medida que su herramienta envejece. Los problemas comunes que puede detectar incluyen:
- • Cobertura amplia del panel
- • Funciones de panel reducidas
- • Borde ondulado en la superposición
- • Control de planeidad del panel: efecto de ballesta
- • Radios de curvatura grandes
- • Calidad degradada en las líneas de post-corte
En muchos casos, los problemas están interrelacionados, como el caso de que su panel se expanda constantemente. Una revisión de sus costillas mayores y menores puede detectar una reducción en la nitidez. En lugar de crear bordes afilados en las crestas de las costillas, las herramientas desgastadas obligan al metal a extenderse. “No puedes ajustar tanto esos dobleces y ese acero extra tiene que ir a alguna parte. Eso es lo que hace que su panel sea amplio”, dijo Schmidt.
“En los grandes, en lugar de tener una buena costilla crujiente, comienza a redondearse. En las costillas menores, en el peor de los casos, se convertirá en una media luna en lugar de una costilla crujiente”, continúa explicando Schmidt. “Esto da como resultado un panel más ancho porque una curva redonda no necesita tanto acero como una curva cerrada”.
Esto se puede detectar visualmente, pero a veces es su cliente de techado quien notará el problema cuando cruce el panel en un sitio de trabajo. “Dirán que simplemente no se siente tan fuerte. Esto se debe a que las curvas no se establecen tan nítidamente. Cuanto más cerradas sean las curvas de un panel, más fuerte será el panel”, explicó Schmidt.

Además, a medida que las herramientas, más específicamente los radios de flexión, comienzan a desgastarse y aflojarse, se necesita más presión para crear una nervadura de ¾”. “A medida que baja más, comienza a perder ángulos, y cuando pierde ángulos, ahí es donde entra en juego su planitud”, explicó Schmidt, y agregó: “Una vez que pierda la capacidad de ajuste, perderá el control de planitud en su panel”.
El control de superposición determina qué tan hermético será un panel. Si un panel tiene un borde ondulado, no proporcionará un solape ajustado. “Para la mayoría de las personas en este negocio, la vuelta lo es todo”, dijo Schmidt. “Si no tienes una vuelta apretada, no es una vuelta hermética”.

Para los instaladores, obtener una superposición ajustada es un desafío si las nervaduras no son consistentes con el panel que se está instalando actualmente, así como con el panel sobre el que se superpone.
Por último, si nota un deterioro en su post-corte, lo más probable es que sea la herramienta. “El troquel de corte no es muy indulgente”, señaló Schmidt. “Lo que va a dar es el panel de calibre 29, no el juego de troqueles de corte. Esto también se aplica si estamos ejecutando cortes previos y cortes para paneles de 2 ', aún verá cierta privación".
Soluciones que no sean de reemplazo
En el mejor de los casos, puede reparar su máquina existente en lugar de reemplazar las herramientas. La primera solución de reparación implica la calibración.
Calibración: “Cuando calibre una máquina, o la mida, estará configurando sus espacios libres verticales, sus espacios libres horizontales, luego querrá establecer sus configuraciones de paso a paso para asegurarse de que se alinee en todo momento”, instruyó Schmidt.
Espacios libres de herramientas verticales y horizontales: El espacio libre vertical de la herramienta es el espacio entre los rodillos superior e inferior en el punto más alejado en el interior (lado de la transmisión) y en el exterior (lado del operador) de la herramienta para cada pasada y en los puntos a lo largo de las secciones más planas de los rodillos donde tiene la parte superior. y rollos de acoplamiento inferiores. El herramental debe calibrarse inicialmente para el grosor máximo del material para el que se diseñó el herramental.
Para calibrar la holgura de la herramienta vertical, primero identificará el grosor máximo del material diseñado y luego ajustará el eje superior para que la galga de espesores máxima del material pase entre los rodillos superior e inferior con un ligero arrastre. Verifique las ubicaciones internas y externas.
Alineación de pase a pase: El herramental de rodillos que ha sido inspeccionado y calibrado dentro de cada pasada de herramental individual debe verificarse para ver si está alineado de pasada de herramental a pasada de herramental. Primero, identifique los tamaños comunes de espaciador/ancho de rollo comenzando desde el lado interior en una serie de pasadas simultáneas de herramientas. Luego, asegúrese de que el espacio en la regla de precisión no exceda 0.010 de pulgada de pasada a pasada. Mida con una galga de espesores para mayor precisión. Tenga en cuenta que los pases de costilla menores generalmente requieren menos espacio.
Como señaló Schmidt, "los ingenieros diseñan en un mundo perfecto, por lo que debe asegurarse de que los espacios sean los mismos en cada pieza de herramienta". Las herramientas adecuadas aseguran que su panel no serpentee a través de la máquina apretado por un lado y suelto por el otro, causando distorsiones en el panel.
Eso no funcionó, ¿y ahora qué?
Si la calibración no resuelve sus problemas de calidad, quedan tres opciones: volver a trazar o recortar las herramientas, reemplazar las herramientas parcialmente o reemplazarlas por completo.
Recorte: Cuando tiene herramientas recortadas, todas las herramientas y espaciadores se retiran de la máquina, se envían a la fábrica y se desmontan, vuelven a trazar, se vuelven a perfilar, se vuelven a cromar, se inspeccionan y se prueban los perfiles. El resultado será un perfil como nuevo, con una contracción del perfil de aproximadamente 0.070 de pulgada.

Las ventajas de un recorte incluyen un costo reducido (alrededor del 50 % de la inversión de un juego nuevo) y un tiempo de entrega reducido de aproximadamente el 50 %.
Una de las desventajas, sin embargo, es la incertidumbre. “Hay un poco de riesgo”, dijo Schmidt. “No sabes con certeza si esos rollos se van a limpiar. Si quita 0.070 de pulgada, pero la herramienta está extremadamente desgastada, o si hay algún daño en alguna parte, eso significa que tendríamos que quitar más de 0.070 o reemplazar la herramienta dañada”.
Cortar más de 0.070 de pulgada es una pendiente resbaladiza porque podría afectar la línea de transmisión de su máquina. “Los cenadores superiores se accionan desde los cenadores inferiores con engranajes rectos”, dijo Schmidt. “Si los diámetros exteriores de las herramientas se reducen demasiado, los engranajes rectos tocarán fondo, lo que impide que las herramientas alcancen la separación de material adecuada. Para corregir el problema, se incurre en un adicional debido al reemplazo de los engranajes rectos superiores”.
Otra desventaja más es la restricción de la modificación una vez que se ha realizado un recorte. “Tu sustrato cambia, tu mercado cambia... y esa herramienta ya está diseñada, no tienes la capacidad de modificarla mucho”, dijo.
Herramientas parciales: El reemplazo parcial de herramientas es una solicitud frecuente de los clientes que han perdido la definición de las nervaduras menores o desean restaurar la planitud del panel reemplazando sus pasadas de sobreformado. Es menos costoso (alrededor del 25 % del costo de un juego nuevo) con un tiempo de entrega menor de 4 a 6 semanas.
Desafortunadamente, no hay garantía de que las nuevas herramientas mezcladas con las herramientas existentes le proporcionen condiciones "como nuevas". Nuevamente, tendrá cambios de diseño limitados y trabajar con alguien que no sea el administrador de equipos originales (OEM) podría complicar la obtención de una estimación precisa.
Reemplazo completo de herramientas: En el caso de un reemplazo completo de las herramientas, se reemplazan todas las herramientas y los espaciadores. Al final, tendrá nuevas herramientas y tendrá la flexibilidad de diseño para incorporar cambios cuando cambie el mercado. También es menos riesgoso obtener de un proveedor que no sea OEM.
Sin embargo, requiere una inversión de capital sustancial y le corresponde al propietario observar de cerca todo el sistema del molino. “Si el conjunto de herramientas está desgastado, es probable que el formador de rodillos también esté desgastado”, dijo Schmidt. “Lo peor que puede hacer es poner un nuevo conjunto de herramientas en una fresadora que necesita ayuda. Por lo general, cuando recomendamos la reconstrucción de una formadora de rodillos, nos ocuparemos de los cojinetes del soporte, los conjuntos de ajuste y la línea de transmisión”.
Aquí hay una lista de lo que querrá hacer en preparación para su nuevo herramental:
- • Reemplace los cojinetes de soporte de la formadora de rodillos
- • Reemplace los conjuntos de ajuste de formadores de rodillos
- • Inspeccione las ruedas dentadas, la cadena, los engranajes rectos y los rodillos impulsores
- • Inspeccione los árboles en busca de desgaste en los chaveteros
Continúe utilizando el mantenimiento preventivo para garantizar una vida útil prolongada y la calidad del producto de su máquina.
Reflexiones finales
Las formadoras de rodillos están diseñadas para durar muchos años y, a menos que experimente un evento catastrófico con una máquina más antigua, probablemente no verá un cambio repentino en su funcionamiento o en la calidad de los productos que produce. “El desafío es que nada de esto sucede de la noche a la mañana”, dijo Schmidt. “Mientras lo ejecutas, es difícil de ver. Es como mi casa; Sé que mi pintura se está desvaneciendo, pero es un declive gradual”.

La solución es tener un programa de rutina de inspecciones y mantenimiento. Para los formadores de rodillos, el nombre del juego es uniformidad, y es mejor vigilar la uniformidad de su calidad para detectar su declive primero antes que su cliente. RF
Nota del editor: esta información fue proporcionada por Ben Schmidt, The Bradbury Group, en una sesión educativa en el Construction Rollforming Show (CRS) de 2019. Esté atento a futuras actualizaciones sobre sesiones educativas en el CRS 2020 en Cincinnati, Ohio, del 10 al 11 de diciembre, en la revista Rollforming. Para más información de la visita del Grupo Bradbury www.bradburygroup.com
Publicado originalmente como "¿Es hora de nuevas herramientas de rodillos?" Edición de verano de 2020 Revista Rollforming.