Автор: Jaswinder Bhatti, Samco Machinery
Прокатне формування використовувалося на дуже повільній швидкості, приблизно 50 футів на хвилину. Тоді було легко обробляти все вручну в кінці лінії. У наші дні валкоутворювачі можуть працювати зі швидкістю від 300 до 500 футів на хвилину. Швидкість може ускладнити роботу з деталями, але також може статися конфігурація деталей, яка стає складнішою в міру розширення можливостей машини.
Як правило, деталі формували в рулонах, а потім вручну вводили додаткові функції та процеси. Сучасні системи формування валків можуть включати деякі процеси штампування, формування, згинання та інші процеси, які не мають нічого спільного з формуванням валків і призначені для повного виробництва однієї деталі. І разом з цими системами постачається складна автоматизація обробки матеріалів.
Перехід від одного процесу до іншого автоматизована обробка матеріалів усуває людські помилки, зокрема, що стосується орієнтації деталей. Автоматизація допомагає перевірити, чи обробляється правильна частина, і орієнтує її для належної обробки. Приклад того ж у галузі опалення, вентиляції та кондиціонування повітря, де після прокатки деталь відправляли на конвеєр, де кондиціонер збирав безпосередньо на ній.
Це також допомагає зменшити залежність від оператора, що збільшує час безперебійної роботи та швидкість формування валків. Система транспортування матеріалів може обробляти набагато швидше, ніж будь-який оператор, особливо коли деталі на лінії великі та важкі. А з великими важкими деталями є аспект безпеки. Неодноразове переміщення та орієнтування деталей вручну протягом дня призводить до втоми та травм операторів.
Використання автоматизованої системи обробки матеріалів значно заощаджує час, особливо з упаковкою та вкладенням. Оператор іноді може втратити підрахунок пробігу деталей, і відправлення можуть відправитися з неточними замовленнями. Можливість підраховувати кількість пробігів, щоб забезпечити правильне виконання замовлень, заощаджує час, як на передньому плані з інвентаризацією, так і з упевненістю, що замовлення не потрібно буде відтворювати та пересилати. Оператору не потрібно постійно вести підрахунок протягом виробничого процесу.
COVID-19 також продемонстрував додаткові переваги автоматизованих систем обробки матеріалів. Виробники повинні були дотримуватися суворих протоколів щодо обмеження кількості людей на робочому місці та дотримання належної дистанції. Ці системи скорочують кількість працівників, необхідних для роботи з прокатним обладнанням, і підтримують стандарти безпеки.
Що потрібно знати
Для виробників, які мають наявні прокатні машини, дуже важливо розуміти, чому і як потрібна автоматизація обробки матеріалів. Більшість магазинів мають обмежений простір на цеховому залі, і включення цих систем може зайняти більше місця, ніж виділяється наразі, що означає, що може знадобитися реструктуризація обладнання. Це вимагає ретельного планування, особливо якщо задіяні вторинні процеси.
Деякі магазини можуть не бачити початкової цінності в додаванні такої системи, особливо з попередніми витратами. Але машина не робить перерв і буде продовжувати роботу з тією ж швидкістю протягом дня. Видаляючи людський елемент і зберігаючи послідовність процесу, виробники можуть очікувати значного збільшення пропускної здатності, іноді до 35 відсотків.
Хоча існує загальний інтерес до автоматизованих систем обробки матеріалів, не всім виробникам потрібні такі системи. Важливо дослідити, чи може цех отримати вигоду від нового обладнання, особливо через значні початкові витрати в багатьох випадках, і які найкращі варіанти для існуючої та майбутньої виробничої діяльності. Чи достатньо обсягу для автоматизованого транспортування матеріалів? І якщо так, то де є вузькі місця в процесі і де найкраще використовувати автоматизацію?
Фронт-енд системи
Існує багато областей формування прокату, де автоматизація може бути перевагою і повинна базуватися на вимогах замовника та специфікаціях машини.
Обробка котушки. Існує багато різних систем обробки котушок залежно від потреб. Як часто потрібно міняти котушки? З якою швидкістю це потрібно зробити? Є кілька варіантів для автоматичної обробки котушки.
Одно- або двосторонній розмотувач можна використовувати для зміни котушок у міру використання матеріалу. Одиничний варіант, як правило, повільніший, але не займає стільки місця в цеху. Двосторонній розмотувач, з однією стороною працює, друга сторона котушки може бути завантажена, щоб мінімізувати час простою.
Комбінація змоточного вагона та підйомника дає змогу завантажувати котушку на катушку, поки розмотувач ще працює, що може бути корисно, коли кран використовується в інших частинах цеху, оскільки оправку можна попередньо завантажити на машину. . Для додаткової ефективності автомобіль з котушками можна поєднати з одинарним або подвійним розмотувачем. Зазвичай котушки доставляються «очо в небо». Потім оператор повинен підняти котушку у вертикальне положення за допомогою крана. Цей процес може бути надзвичайно ризикованим, оскільки є ймовірність зісковзування котушки. Але пендер безпечно переведе котушку у вертикальне / вертикальне положення. З іншого боку, комбінація автомобіля для підйому і котушки також може безпечно розвантажувати частково використані котушки, повертаючи їх у положення «око до неба» з вертикального положення, яке потрібно забрати.
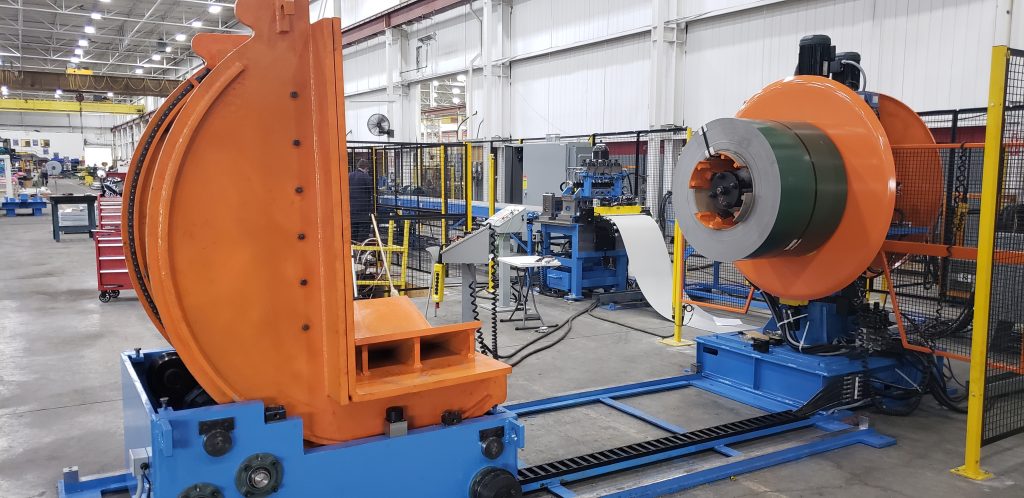
Комбінація змоточного вагона та верхньої частини дозволяє завантажувати котушку на катушку, поки розмотувач ще працює,
Акумулятор. Котушка, яка відривається від розмотувача, надходить в акумулятор, де подається в валкоутворювач. Коли вся котушка знаходиться в акумуляторі, котушку можна замінити без зупинки процесу формування рулону. Після заміни котушки матеріал знову потрапляє в акумулятор. Ця автоматика може заощадити до 10-15 хвилин на зміну котушки.
Кінцевий зварювальний апарат. Це дозволяє оператору з’єднати задню кромку робочої котушки і передню кромку нової котушки, щоб заощадити час на подачу котушки по всій лінії. Це може заощадити час простою та обмежує пошкодження (зменшуючи брак) через ручну подачу.
Системи підбору та розміщення. Замість того, щоб вручну подавати одну заготовку за раз, вона збирає та розміщує попередньо нарізані матеріали на електричному конвеєрі. Він може відповідним чином вибирати деталі для правої та лівої руки. Системи підбору та розміщення можна використовувати для правильного орієнтування деталей для пост-процесів, таких як згинання або штампування.
Back-End системи
Як виробники мають справу з деталлю після завершення процесу формування валків? Існують різні варіанти автоматизованої обробки матеріалу, які можна інтегрувати в кінці лінії формування валків для підвищення ефективності.
Гнізда. Це використовується, оскільки готовий продукт зривається з лінії на високих швидкостях. Він збирає та вкладає групу або пачку готової продукції, як правило, для коней і колійної промисловості, щоб перемістити їх на пакування та відправлення. Гнізда усувають потребу в декількох робітниках на кінці лінії формування валків.
Штабелери. Ця система транспортування матеріалів укладає готові деталі в кінці лінії формування валків і запрограмована на переміщення штабеля з попередньо визначеною кількістю деталей на штабель у зону для вивезення вилковим навантажувачем.
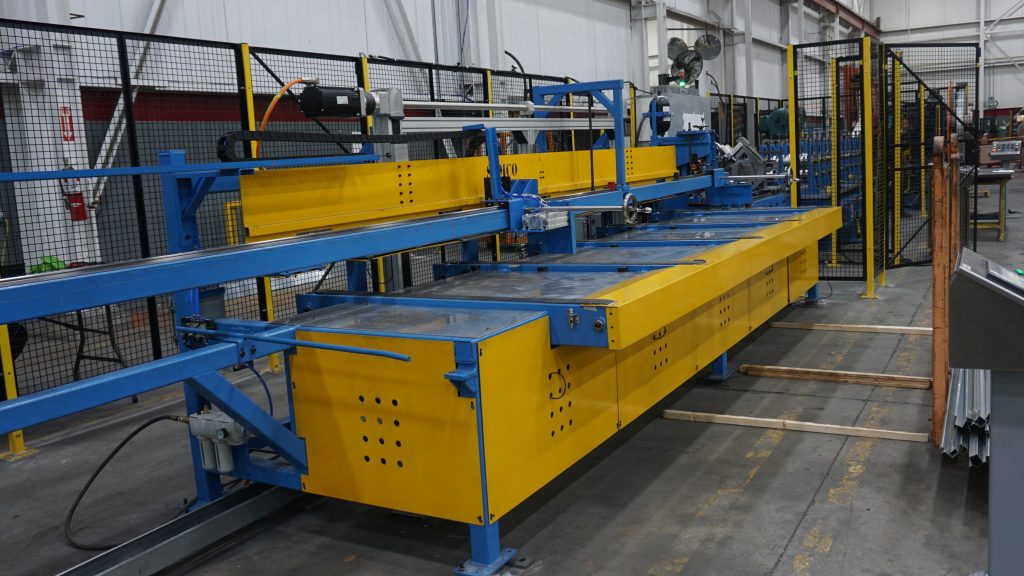
Гніздо виключає необхідність використання кількох робітників на кінці лінії формування валків.
Комплектувальники. Після того як деталі знімаються з рулона, вони вкладаються в міні-пучки. Пакетувальники автоматизують обробку міні-пакетів і автоматично створюють попередньо запрограмовані головні пакети, які готові до відвантаження на основі замовлень деталей і партій. Головний підйомний стіл піднімається, щоб отримати перший шар продукту з машини, і опускається в міру накопичення стопок. Потім вони з’єднуються в один блок для відправлення. Після того, як цей головний пучок завершено, підйомний стіл опускається до кінця і подає готовий пучок на кінцевий вихідний роликовий конвеєр. Ця система вантажопідйомності виключає ручне підняття упакованих пачків і зменшує травми через підйом і поворот важких згрупованих деталей.
Упаковка. Після того, як деталі знімаються з рулонного формувача і з’єднуються в пучки або штабеля, необхідна належна упаковка, щоб деталі прибули безпечно без пошкоджень. Системи пакування можуть включати термоусадкову упаковку, додавання пластикового або паперового аркуша між кожною частиною, додавання прокладки та обв’язки або пухирчасте обгортання пачки, щоб вона була готова до завантаження на вантажівку.
Наступна хвиля інновацій
Оскільки існує безліч різних автоматизованих систем обробки матеріалів, важливо мати систему моніторингу. Сучасні машини настільки швидкі, що оператори не можуть встигати за тим, як швидко обробляються деталі, що ще важче встигати за тим, щоб деталі виготовлялися належним чином.
Додавання перевірок якості або моніторингу до процесів – це те, що ми все частіше будемо бачити в наших системах формування прокату. Здатність автоматизованої системи обробки матеріалів розпізнавати всі деталі, виявляти несправні деталі та відокремлювати їх перед комплектуванням і відправкою буде значною економією витрат і часу.
Новітні та найкращі автоматизовані системи обробки матеріалів можуть полегшити життя будь-якого виробника. Менше працівників потрібно для ручної обробки деталей у процесі формування прокату, що усуває проблеми з безпекою та звільняє працівників для інших процесів. Додавання навіть одного або двох з цих параметрів може зробити процеси формування валків швидшими та надійнішими. Не кожному магазину потрібне найсучасніше обладнання, але важливо дивитися на наявні та майбутні потреби, щоб ви могли розвиватися у обладнанні. Налаштування лінії формування валків повинно ґрунтуватися на валкоутворювачі та його можливостях, потребах у виробництві деталей, а також на розумінні початкових витрат та рентабельності інвестицій. РФ
Джасвіндер Бхатті є віце-президентом з розробки додатків Samco Machinery, Торонто, Онтаріо; www.samco-machinery.com.