■ By Sharon Glorioso
Editor’s Note:
In reviewing what articles were the most popular on our website, ConstructionMagNet.com, we rounded up the top ten, updated information, and are republishing those articles throughout this year in our various construction magazines. One of the top 10 includes the article that follows, first appearing in the June/July 2014 issue of sister publication, Metal Roofing Magazine.
More and more roofing contractors these days are answering “yes” to that question. Manufacturing independence, waste management, shipping considerations and other factors paint a compelling case for contractors looking to buy a roll former and produce their own panels. But it’s not that simple — additional manufacturing costs, employee training, warehousing and a different set of transportation considerations must be weighed before pulling the trigger on this significant purchase.
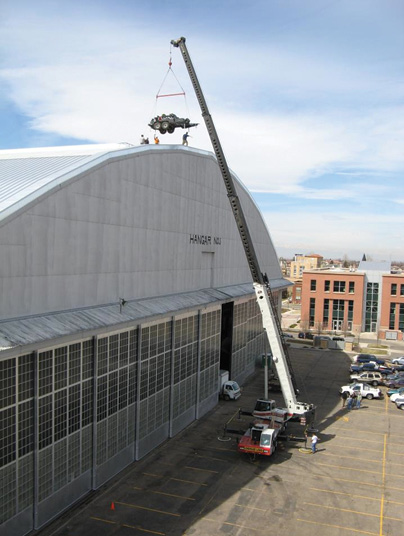
Mike Milliman of Gutter Supply Inc. decided it was worth it. Gutter Supply has been selling New Tech Machinery’s gutter machines for years and has had such a positive experience with their equipment. The company recently became a distributor for New Tech’s roof panel machines. “There are so many benefits for companies to purchase their own machinery,” Milliman says. “Just not having to depend on anyone else is a big advantage. It saves time as well as money.”
Ken McLauchlan, regional manager with Drexel Metals, agrees, and says it’s about controlling what kinds of projects you want to take on. “You can control your own destiny and have the flexibility of what jobs you can do — and be confident that you are putting out a better product,” he says.
For 42 years, Roll Former Corp., of Chalfont, Pennsylvania, has designed and developed custom machinery for companies looking for a roll-forming application. “We design our custom equipment from scratch and we offer about 25 standard products,” said John Dumke, director of sales and marketing for Roll Former Corp. Dumke says that roll forming has many cost advantages over brake forming and preformed panels, including:
• No expensive shipping and crating of long panels. Coils are delivered right to the shop or jobsite
• No panel shipping damage, and delays are minimal
• Less labor and waste
• The ability to work on your own schedule, not the factory’s
• Form perfect panels to any length.
Additionally, Bruce Pearson, with Zimmerman Metals, has been in the business for more than 40 years, and he says that you can reduce your cost of doing business by using a portable roll former in many ways. “On-site fabrication eliminates shipping damage, you don’t have to worry about packaging materials, sizing errors and the panels can be custom manufactured. Also, as you make your panels on site, you don’t have to worry that the manufactured panels will get damaged laying around on the jobsite,” he says.
In-House vs. Portable Roll Forming Equipment
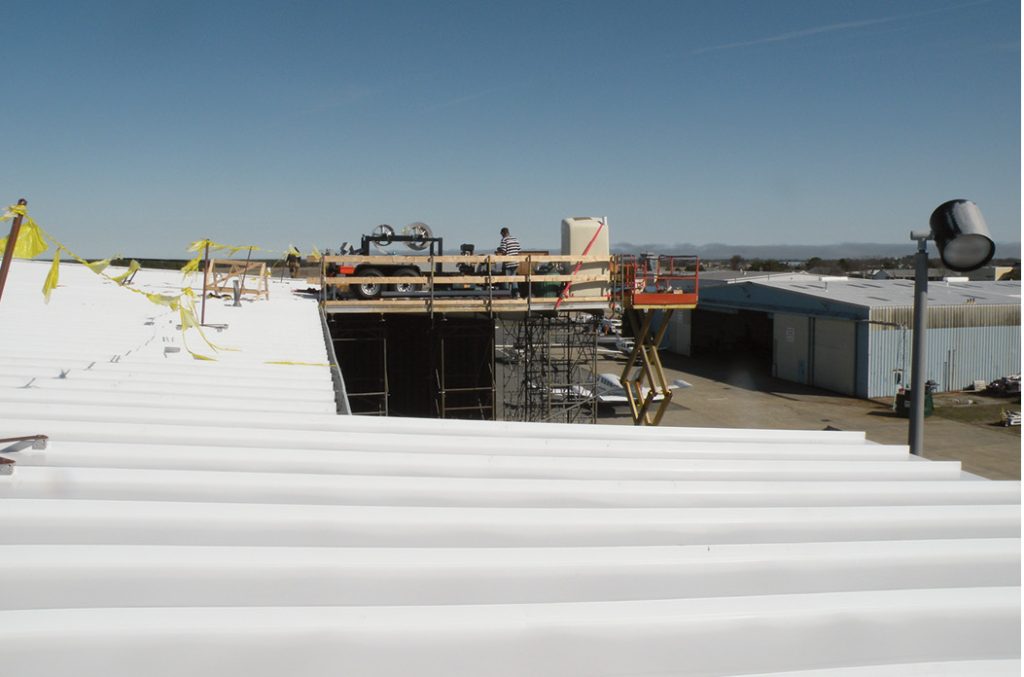
Ready to roll your own? Your next decision will be to choose between the two distinct types of roll formers — portable and in-house [stationary] machines. In-house machines are usually larger units designed and built for high-production rates. Portable roll formers are smaller for simpler transportation and tend to be more flexible in their ability to produce a variety of panel profiles.
For in-house manufacturers, you don’t have to keep your machine busy to justify its expense, as they are built for increased orders and high-production rates.
However, portable roll formers tend to save on transportation costs — they save on packaging and freight costs while giving the roofer the ability to reduce the time of a project, instead of ordering factory-formed panels. As an added bonus, onsite panel fabrication eliminates the possibility of shipping damage to panels, miscalculated sizing, etc. Also, onsite roll formers can produce panel lengths varying in size required by the specific roof, as they are not regulated by shipping rules.
What It Costs
So you’ve decided to open up the checkbook and buy a roll former. Will it be worth the investment? Cost varies, and your priorities will drive just how large a check you will need to write.
“There’s the entry level and the commercial level. But having the flexibility and the ability to cut the middle man out may be beneficial to your business,” says Drexel’s McLauchlan. “The entry level roll former may start in the low $20,000 range, where the very specific commercial machines might be as high as $150,000. But being able to diversify your jobs will be worth the cost.”
There are a number of companies in the industry that will work with contractors on equipment financing. Another option would be to lease equipment. Leasing payments are much less expensive of the total purchase price of a roll former and it can be a pre-tax expense. Leasing also allows for upgrades and equipment add-ons.
According to Pearson at Zimmerman Metals, they train on maintenance and adjustment of their machines. “We provide training on all of our equipment. You can either do it on-site in our factory, or we will send one of our technicians out to you to do the training and it usually only takes one day. We don’t charge for this on any new machines that are purchased,” Pearson said.
Dumke, at Roll Former Corp., says they offer training as well. “We do this in two ways; we offer free training at our facility, or if we send a technician to the customer’s location, we do charge for that cost. Either way, we will make sure that you know how to operate our custom machine.”
As with any significant purchase, a contractor looking to purchase a roll former should shop around, and consider not only the price but quality reputation, warranties and service.
Additionally, Pearson says to do reference checks. “It’s also important to know how long they have been building their machines; check to see if they offer training, see where they make their equipment. I personally prefer American made, but make sure it is a quality company with a quality product. We offer a two-year warranty on our machines, but we never have any problems. I built my first machine 24 years ago, and the owner today of this machine has only replaced one part in 24 years,” he said.
Always Evolving
Today, portable roll formers tend to be more advanced and use modern technology that can produce quality panels that are competitive with in-factory roll forming machines. Portable roll formers can cut metals more quickly, without any waste. Many roll formers sold today feature computer controllers software that offers users more options and benefits than in the past. Many offer proximity sensors, multiple-length memory storage, batch and length control, and some even recognize coil color for state-of-the-art user-friendly settings.
Another key distinction among different types of roll formers is multi-panel vs. fixed panel machines. Rich Small of Englert Inc., in Perth Amboy, New Jersey, reports seeing more and more of the former.
“We are seeing more of the multi-panel options being sold, as contractors want to be able to diversify their jobs, and get more of the market share in their business,” Small says. “There are also more customized projects being sought by both residential and commercial roofing contractors.” RF
Originally published as “Are you ready to roll your own?” Spring 2021 issue Rollforming Magazine.