Von Karen Knapstein
Mit derzeit 6.8 Milliarden US-Dollar ist die Carport-Branche eine wachsende Branche. Die Verbraucher erkennen, dass die Wahl einer Struktur mit Metallrahmen zur Aufbewahrung eines Fahrzeugs, überschüssiger „Sachen“ oder sogar Vieh eine nahezu sofortige Lösung für ihre Lagerprobleme darstellt. Als wachsende Branche bietet sie Chancen für Rollformer.
Eine wachsende Industrie
Rollformsysteme für Metall entwirft, fertigt und baut Paneellinien, Zierlinien und Zubehörteile, die beim Rollformen von Carportkomponenten und anderen leichten Paneelen verwendet werden. Firmenpräsident Bill Griffin verrät: „Die Carportbranche als Ganzes verzeichnet weiterhin ein Rekordwachstum. Dieses Wachstum hat die bestehenden Komponentenlieferanten und -hersteller belastet. Dies hat viele in der Branche dazu veranlasst, die Fertigung intern zu verlagern, um die Vorlaufzeiten zu verkürzen und die Materialkostenerhöhung auszugleichen. die Qualität der Produkte für ihre Kunden und Crews zu erleichtern und besser zu kontrollieren.
Trend: Automatisierung
„Wie viele Branchen“, fährt Griffin fort, „sieht die Carport-Branche insgesamt eine Verlagerung hin zu einer stärkeren Automatisierung. Immer mehr Carport-Hersteller stellen von Abkantpressen und Falzmaschinen auf Rollformanlagen um. Die exponentielle Geschwindigkeitssteigerung trägt dazu bei, die ständig steigenden Arbeitskosten und Anforderungen an ihre Produkte auszugleichen. Ich glaube, dass die Branche weiterhin Wachstum beim Formwalzen und Strukturwalzen verzeichnen wird.“

Das Biegen und Falten von Zierleisten mit Pressen und Abkantpressen erfordert viel mehr Zeit und Arbeit als das Rollformen der Komponenten. Wenn die Arbeitskosten zu den Material- und Einrichtungskosten hinzugerechnet werden, kann der Preis für die Herstellung der Komponenten den Verkaufspreis übersteigen. Die Automatisierung führt zu einem höheren Durchsatz und einer höheren Produktion bei gleichzeitiger Erhöhung der Genauigkeit. „Kunden, die Teile rollformen, sehen in der Regel eine 10- bis 20-fache Steigerung der Teileproduktion im Vergleich zu einer herkömmlichen Herstellungsmethode mit einem Falzapparat oder einer Abkantpresse“, erklärt Griffin. „Sie profitieren auch von konsistenteren Teile- und Winkelmessungen.“
Rohrformung
Ralph Girkins von Universelle Rohr- und Rollformgeräte hilft uns dabei, den Prozess des Formens von Rohren aus aufgewickeltem Stahl zu untersuchen. Girkins, der „dieses Geschäft seit 40 Jahren zu seinem Geschäft macht“, gründete 1984 Universal Tube & Rollform Equipment in Perrysburg, Ohio. 2005 gründete er zusammen mit Ken Metzger und Laura Smirin die Universal Controls Group (UCG). bieten ihren Kunden mehr Möglichkeiten beim Kauf von Umformmaschinen. Heute bietet das Unternehmen einen der größten Lagerbestände an Metallbearbeitungsmaschinen, Maschinenüberholung, Außendienst vor Ort, neue Steuerungen, Antriebssysteme und Kauf- und Verkaufsoptionen für überschüssige Maschinen.
Girkins sagt: „Wir haben 15 Rohrwalzwerke auf Lager und etwa 60 Rollformmaschinen, einschließlich gebrauchter und überholter Ausrüstung. Viele neue Leute wollen gebrauchte Geräte, um loszulegen. Sobald sie anfangen, damit Geld zu verdienen, wollen sie eine neue Maschine, weil sie schneller werden wollen. Wir können alle Maschinen und Anlagen liefern, die Sie für ein Rohrwerk benötigen.“ Er sagt, dass die typischen Kosten für eine neue Rohrmühle zwischen 600,000 und 800,000 US-Dollar liegen, abhängig von den Maschinen und Werkzeugen, die in der Aufstellung enthalten sind. Eine gebrauchte Maschine ist etwa die Hälfte der Investition.
Coil to Cut – So wird’s gemacht
Wahrscheinlich sind Sie bereits rollende Komponenten, die beim Bau von Carports verwendet werden, da sie die gleichen sind wie die, die in anderen Metallgebäuden verwendet werden. Hutkanal, üblicherweise aus 26- und 29-Gauge-Stahl gewalzt, wird verwendet, um Dach- und Wandpaneele zu stützen. U-Profile, die für Streben und Stützen verwendet werden, tragen zur Verstärkung der Struktur bei. Paneele und Verkleidungen werden schnell und einfach von 24-Gauge- bis 28-Gauge-Coilstahl gewalzt. Unternehmen wie ASC Machine Tool, Metal Rollforming Systems und The Bradbury Company stellen Maschinen her, die mehrere Profile walzen, wodurch die Notwendigkeit mehrerer Beschnittmaschinen entfällt.
Das Rollformen von Rohrstahl ist etwas komplizierter als das Rollformen von Platten und Verkleidungen. Die für Carportrahmen verwendeten Messgeräte sind schwerer – hauptsächlich 12- und 14-Gauge-Stahl. Schläuche messen normalerweise 2" bis 2 1/2". „Welches Messgerät Sie verwenden, hängt von der Größe der Struktur ab, die Sie bauen. Je größer die Struktur, desto schwerer die Rahmenstärke, die Sie verwenden müssen“, erklärt Girkins.
Der Prozess umfasst mehr Schritte und mehr Ausrüstung ist an der Herstellung von Stahlrohren beteiligt. Die Hochgeschwindigkeitsausrüstung läuft mit einer Geschwindigkeit von 150-250 Fuß pro Minute, obwohl Girkins sagt, dass sie einige Mühlen herstellen, die mit bis zu 1,000 Fuß pro Minute laufen.
Um aus einer flachen Stahlrolle ein Rund- oder Vierkantrohr zu machen, sind mehrere Schritte erforderlich. Wenn das Rohr Löcher oder Schlitze benötigt, werden diese in den Stahl gestanzt, bevor er zu einem Rohr geformt wird. Die Universal Controls Group stellt Maschinen her, die den Flachstahl vermessen und Löcher und Schlitze darin stanzen. „Es ist viel einfacher, Löcher in das noch flache Material zu stanzen“, sagt Girkins.
Die Stahlcoils werden zu einem langen Endlosband stumpfgeschweißt und auf einen Akkumulator geladen. Durch das Zusammenschweißen der Stoßenden entfällt die Notwendigkeit, die Maschine neu einzufädeln, es reduziert Abfall und verkürzt die Umrüstzeit zwischen Coils. Es verringert auch das Risiko einer Beschädigung der Matrizen durch falsch eingefädelten Stahl.
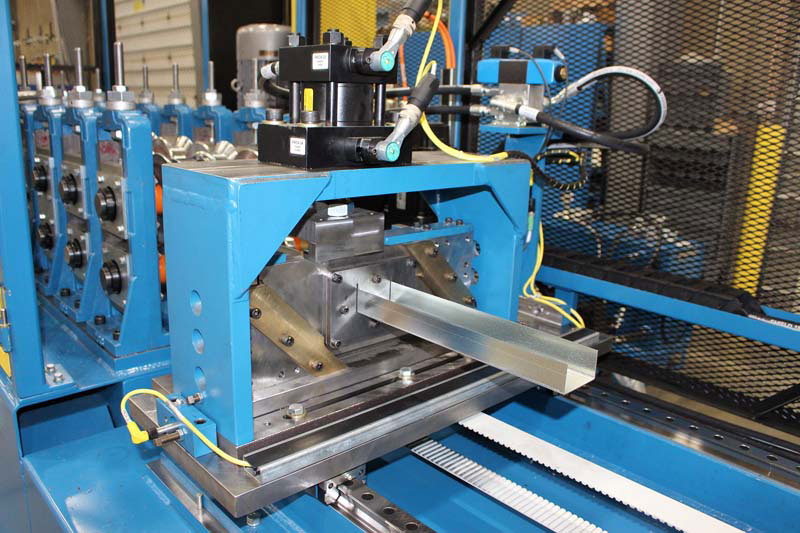
Vom Akkumulator wird das Coil in das Walzwerk in eine Treibrolle geführt. „Die Mühle steht nie still“, erklärt er. „Die Theorie ist, dass Sie die Rohrmühle nie schließen. Sie verwenden das angesammelte Material, um es am Laufen zu halten, bis Sie mit dem Tag fertig sind.“
Während die Flachspule durch die Maschine läuft, wird sie nach oben und unten geformt, bis sie ein Rohr ergibt. Es ist, als würde man den Streifen durch einen Trichter ziehen. Vor dem Schneiden durchläuft das Rohr einen Hochfrequenzschweißer. „Eine Hochfrequenzschweißung wird nicht mit einem Schweißbrenner geschweißt“, stellt Girkins klar. „Der Schweißer erhitzt die Kanten und die Kanten werden zusammengedrückt. Es ist eher geschmiedet als geschweißt.“
Die Kanten werden auf etwa 1800 Grad erhitzt, was so heiß ist, dass die vorverzinkte Zinkschutzschicht den erhitzten Bereich abbrennt und eine Verstimmung verursacht. Mit einem Drehwerkzeug wird das gestauchte Material abgeschält, wodurch der Bereich wieder glatt wird. Ein Schweißbrenner und ein automatischer Sprühschweißer werden verwendet, um die schützende Zinkschicht auf der Oberseite der Naht wieder aufzubringen.
Nach dem erneuten Auftragen der Zinkbeschichtung durchläuft das Rundrohr eine 20'-Kühlwanne, wo es mit Kühlmittel (Wasser) besprüht wird. Die Standardmethode zur Herstellung des Vierkantrohrs, das zum Einrahmen von Carports verwendet wird, besteht darin, ein rundes Rohr herzustellen und es dann in seine quadratische Form zu drücken.
Normalerweise sind drei Durchgänge durch das Maßwalzwerk erforderlich, um die quadratische Form zu erhalten. Nachdem es die Turkshead-Einheit durchlaufen hat, wo es begradigt und quadriert wird (falls gewünscht), läuft es durch einen Encoder, wo es gemessen wird. Dann geht es entweder durch eine fliegende Säge oder einen Abschneider. „Viele Carport-Leute verwenden jetzt fliegende Kaltsägen; Es ist eine schöne, saubere und einfache Methode zum Schneiden“, sagt er. „Es gibt keine Verformung im Rohr, wenn die Klinge durchgeht, und es gibt keinen Grat.“ Weder das Material noch die Maschine stoppen, um die Schnitte auszuführen. Eine Matrize bewegt sich mit der gleichen Geschwindigkeit wie das Rohr entlang des Rohrs und führt den Schnitt aus, wenn sie das Signal vom Encoder erhält.
An diesem Punkt werden die Bahnen, falls erforderlich, als sekundärer Arbeitsgang durch eine Stauchmaschine geführt. Wenn das Rohr für eine Slip-Fit-Konstruktion verwendet werden soll, werden die Längen durch einen Presser geführt, um ein Ende des Rohrs so weit zusammenzudrücken, dass es in das Ende eines anderen Rohrs gleitet.
An diesem Punkt sind die Rahmenkomponenten fertig und bereit für Ihren Kunden.
Zusammenfassung
Rohrmühlen sind eine große Investition und nehmen viel Platz ein; Sie können gut zu Ihrem Shop passen oder auch nicht. Wenn Sie jedoch bereit sind, in eine eigene Mühle zu investieren, um diesen wachsenden Markt zu beliefern, gibt es viele Unternehmen, die bereit sind, Sie zu führen. RF