Von Kenneth P. Lambert, Jr.
Der griechische Philosoph Heraklit von Ephesus soll den Satz „Die einzige Konstante im Leben ist der Wandel“ geprägt haben. Veränderungen finden immer statt, ob wir wollen oder nicht. In der Fertigungsbranche, wie in fast allen Bereichen der Geschäftswelt, bemühen wir uns, den Veränderungen der Märkte, wirtschaftlichen Bedingungen und anderen Kräften, die sich unserer Kontrolle entziehen, immer einen Schritt voraus zu sein.
Es gibt jedoch eine Form der Kontrolle, die wir geltend machen können und sollten. Dies ist eine selbstgesteuerte Veränderung zum Besseren in unseren Organisationen. Wie können wir auf bewusste und durchdachte Weise positive Veränderungen auslösen und steuern? Es gibt einen Begriff, der einigen Fertigungsprofis bekannt sein könnte: Kaizen. Dieser Begriff basiert auf den japanischen Wörtern „kai“ (Veränderung) und „zen“ (zum Besseren) und ergibt „Veränderung zum Besseren“, was manchmal als „kontinuierliche Verbesserung“ oder „tägliches Hinarbeiten auf einen idealen Zustand“ interpretiert wird.
Natürlich ist das die Art von Veränderung, auf die wir alle hoffen, aber hinter dem Begriff „Kaizen“ steckt mehr als Wunschdenken. Es bedeutet mittlerweile „einen systematischen Ansatz zur Verbesserung des Geschäfts“ und erfordert Führung, Engagement und Selbstdisziplin. Die Gemba Academy, eine Schulungsorganisation, die sich auf kontinuierliche Verbesserung konzentriert, erklärt, dass es für Organisationen unerlässlich ist, eine „Kultur des Kaizen“ zu entwickeln, wenn sie langfristige Erfolge bei ihren Bemühungen um kontinuierliche Verbesserung erzielen wollen. Mit den Worten des Gründers des Kaizen-Instituts, Masaaki Imai, „Alltägliche Verbesserung. Jeder Verbesserung. Überall Verbesserung.“
Das Konzept von Kaizen entstand in den Jahren nach dem Zweiten Weltkrieg, als die US-Streitkräfte beim Wiederaufbau der japanischen Industrie halfen. Angesichts des Mangels an Zeit und materiellen Ressourcen waren sofortige, drastische Verbesserungen nicht durchführbar. Stattdessen wählten sie einen Ansatz, der inkrementelle, kontinuierliche Veränderungen betonte. Ein Schlüsselelement bestand darin, die vorhandene Belegschaft einzubeziehen und das praktische Problemlösungswissen dieser Mitarbeiter zu nutzen.
Aus diesem Moment in der Geschichte mussten Lehren gezogen werden. Kann eine Organisation ihre Abläufe trotz begrenzter Ressourcen erheblich verbessern? Toyota stellte fest, dass die Antwort ein klares „Ja!“ war. Tatsächlich wurde die Idee von Kaizen eng mit dem „Toyota Production System“ verbunden – einer Reihe von Managementphilosophien, die von Toyota entwickelt wurden, um Verschwendung zu vermeiden. Diese Prinzipien, die großen Wert auf das Engagement von Einzelpersonen im gesamten Unternehmen legen, werden von Jeffrey Liker in seinem Buch „The Toyota Way – 14 Management Principles from the World’s Greatest Manufacturer“ beschrieben.
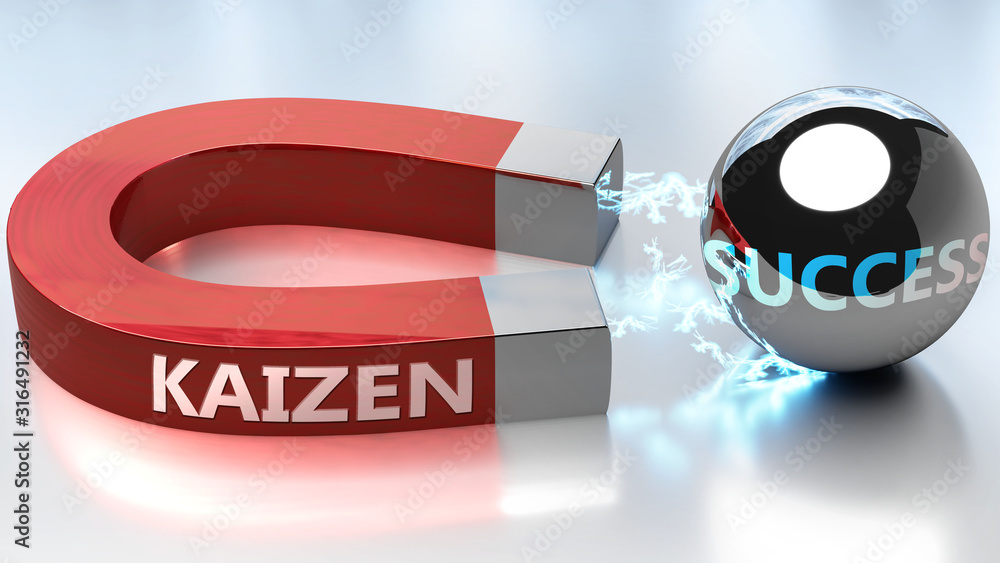
Jikoda
Eine Denkweise, die Mitarbeiter anvertraut und erwartet, selbstbewusste Problemlöser zu werden, hat konkrete und unmittelbare Anwendungen für den kleinen Hersteller. Das Toyota-Prinzip von jikoda – Anhalten des Prozesses zur Behebung von Problemen – veranschaulicht diese Denkweise. Jikoda befähigt die Mitarbeiter nicht nur, sondern fordert sie sogar auf, den Produktionsprozess anzuhalten, sobald sie ein Problem sehen. Das Problem kann ein Defekt in einem Teil oder eine Abweichung vom Standard sein. Es erscheint kontraintuitiv, einen Produktionsstillstand als Schlüssel zur Abfallreduzierung zu betrachten. Wenn jedoch die Produktion fortgesetzt wird, während ein Problem übersehen oder verheimlicht wird, wird das Problem in Form von Ausfällen, außerplanmäßigen Wartungsarbeiten, Materialverschwendung oder einem beschädigten Ruf auf der ganzen Linie verschlimmert. Die Ermutigung der Mitarbeiter, die Produktion anzuhalten, wenn ein Fehler entdeckt wird, bringt langfristige Vorteile. Es verhindert, dass sich Fehler im Endprodukt festsetzen. Es gibt den Mitarbeitern auch ein Verantwortungsgefühl und bindet sie wirklich in ihre Haupttätigkeit ein: dem Kunden einen Mehrwert zu bieten.
Heijunka
Ebenso Toyotas Konzept von heijunka erscheint zunächst kontraintuitiv. In einer Umgebung, in der die Just-in-Time-Lieferung von Produkten als ultimativer „Lean“-Ansatz gilt, schlägt heijunka vor, dass eine Nivellierung von Produktionsvolumen und Produktmix wilden, reaktiven Schwankungen im Produktionsfluss vorzuziehen ist. Systeme, die stark auf Bedarfsspitzen und -täler reagieren, neigen dazu, Intervalle mit Unterauslastung und Überauslastung von Ausrüstung und Personal zu verursachen. Das Letzte, was ein Hersteller will, sind ungenutzte Geräte, aber er möchte auch nicht, dass der Ausfall von überlasteten Geräten zu ungeplanten Abschaltungen führt. Unternehmen, die eine „Kaizen-Kultur“ anstreben, sollten auch Umstände minimieren, die zu überlasteten, unmotivierten Mitarbeitern führen, die nicht länger nach Verbesserungen suchen, oder auf Produktionsmängel aufmerksam machen. Ein moderater Volumenstrom kann Kunden manchmal dazu veranlassen, auf Produkte zu warten, schützt aber auch vor ungeplanten Stillständen und ungewollten Qualitätsmängeln. Diese Ergebnisse bieten einen Mehrwert für Ihre Kunden.
Kaizen-Ereignis oder Training
Eine andere Möglichkeit, Kaizen zu sehen, ist die Form eines „Kaizen-Events“ oder eines „Workouts“ – ein 1- bis 5-tägiger Prozess, der darauf ausgelegt ist, von den praktischen Erfahrungen der Teilnehmer zu profitieren. Dr. Richard Chua, Professor und zertifizierter Lean Six Sigma-Trainer, definiert eine Kaizen-Veranstaltung als „gut organisierte, strukturierte und moderierte Veranstaltung zur Verbesserung eines Arbeitsbereichs, einer Abteilung, eines Prozesses oder eines gesamten Wertstroms“. Mit einer „Kaizen-Kultur“ als Grundlage versucht eine Kaizen-„Veranstaltung“, Interessengruppen in der gesamten Organisation einzubeziehen.
Ein Kaizen-Event ist dann sinnvoll, wenn eine schnelle Analyse des Problems möglich ist und mit einfachen Tools sofort Verbesserungen vorgenommen werden können, ohne dass eine rigorose Datenanalyse erforderlich ist. Um das Beste aus dieser Zeitinvestition herauszuholen, sollte eine Kaizen-Veranstaltung unter der Leitung eines Moderators stattfinden, der in Operational-Excellence-Tools geschult ist. Der Moderator leitet den Prozess, sodass die richtigen Fragen gestellt werden und die Zeit sinnvoll genutzt wird. Zunächst müssen das Ziel und der Umfang der Veranstaltung definiert werden. Zum Beispiel:
• Einführung von Qualitätsprüfungen und Rechenschaftspflicht in den Prozess (Jikoda)
• Arbeitsablauf verfeinern (z. B. Anwendung des Heijunka-Prinzips)
• Identifizieren der Grundursache eines wiederkehrenden Qualitätsproblems
• Rationalisierung des Geräteaufbaus
• Neuorganisation eines Arbeitsbereichs zur Verbesserung der Effizienz.
Es kann nicht stark genug betont werden, dass ein solches Ereignis von Menschen abhängt. Es handelt sich um eine von Menschen angetriebene und auf Menschen ausgerichtete Übung, daher müssen die richtigen Personen zur Teilnahme eingeladen werden. Dazu gehören die Bediener, Mitarbeiter in der Fertigung und andere Interessengruppen, die einzigartige Einblicke liefern können. Andere im Wertstrom können eine Vielzahl von Perspektiven einbringen. Sogar Kunden können beteiligt sein. Dies sind genau die Menschen, die sich auf den durch den betreffenden Prozess geschaffenen Wert verlassen, sodass ihre Beteiligung außerordentlich stark sein kann.
Sobald ein gewünschtes Geschäftsergebnis definiert ist, kann eine Vielzahl von Problemlösungstechniken eingesetzt werden. Zum Beispiel:
• Abbildung des Flusses von Teilen oder Transaktionen in einer Einrichtung, um zu verstehen, was tatsächlich passiert
• Ein „Gemba Walk“ – Spaziergang durch die Produktionshalle (Gemba = „der Ort, an dem Wert geschaffen wird“)
• Prozess- und Wertschöpfungsanalysen, um festzustellen, welche Schritte wertschöpfend sind und welche nicht
• Entwicklung von Ursache-Wirkungs-Diagrammen
• „5 Warum“ – 5 Mal hintereinander nach dem „Warum“ fragen, um die eigentliche Ursache eines Problems aufzudecken
• 5S-Übungen zum Sortieren und Ordnen von Gegenständen unter der Prämisse, dass es für alles einen Platz gibt und alles an seinem Platz sein sollte.
Nach Abschluss der Veranstaltung sollten die Teilnehmer mit einer Liste von Empfehlungen für konkrete, umsetzbare Lösungen herauskommen, die sofort in die Praxis umgesetzt werden können. Da diese Lösungen von den Stakeholdern selbst entwickelt wurden, ist die Akzeptanz für die Umsetzung typischerweise höher.
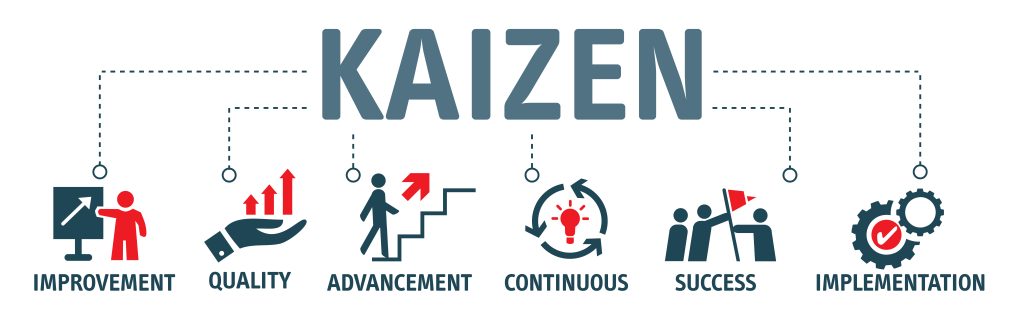
„Kontinuierliche Verbesserung“ setzen
Zum Üben
Während große Hersteller häufig Experten beschäftigen, um kontinuierliche Verbesserungsbemühungen wie Kaizen-Veranstaltungen zu leiten, verfügen kleinere Hersteller häufig nicht über den Hintergrund in diesen Disziplinen oder die Kapazität, engagierte Mitarbeiter mit diesen Fähigkeiten einzustellen.
Glücklicherweise gibt es viele Ressourcen zur Verfügung. Es gibt Trainingsprogramme, Seminare, Videoserien und Bücher, die sich auf diese Techniken spezialisieren. Viele Universitäten bieten Produktionserweiterungen an, die lokalen Unternehmen kostengünstige Beratungs- und Schulungsdienste anbieten. Natürlich gibt es qualifizierte Berater, die bereit sind, mit Herstellern zusammenzuarbeiten, die bereit sind, ihre Reise zur kontinuierlichen Verbesserung zu beginnen.
Zusammenfassung
Viele dieser Grundsätze können sofort umgesetzt werden, um positive Effekte zu erzielen, aber es ist hilfreich, die kontinuierliche Verbesserung als Marathon zu betrachten. Sich zu einem Marathon zu verpflichten, erfordert eine Marathon-Denkweise. Jeder, der einen absolviert hat, weiß, dass es eine lebensverändernde Erfahrung ist. Die harte Arbeit, die erforderlich ist, um dieses langfristige Ziel zu erreichen, zahlt sich letztendlich aus. Ebenso ist Kaizen mehr als nur das Kaizen-Event oder „Workout“. Ein Kaizen-Training ist genau das… ein Training. Es ist gut für dich. Es wird praktische Lösungen für Probleme liefern. Aber es ist nicht der ganze Marathon. Wie ein Experte für kontinuierliche Verbesserung erklärt, lösen Kaizen-Events spezifische Probleme, aber was noch wichtiger ist, sie lehren Mitarbeiter, wie sie Problemlöser werden können. Sie tragen dazu bei, die Leidenschaft für kontinuierliche Verbesserung in Ihrem Team zu fördern. Teams, die an einer „Kaizen-Kultur“ teilnehmen, übernehmen Verantwortung für ihre Aufgaben mit dem Ziel, Mehrwert für den Kunden zu schaffen. Darum geht es: eine Kultur zu entwickeln, in der Menschen – jeder in der Organisation – vertraut, befähigt und ermutigt wird, eine aktive Rolle bei positiven Veränderungen zu spielen. Alle arbeiten mit vollem Einsatz daran, einen Idealzustand herbeizuführen: maximalen Wert für den Kunden. Rf