De los sistemas SmartBuild
Resumen
Utilizaron una nueva tecnología de automatización de Sistemas SmartBuild™ (SBS) que les permitió rodar cada pieza de material de armazón de una sola máquina formadora de rollos. Estas no eran piezas 'tontas' como las que se podían comprar de un fabricante típico de pernos de acero; cada parte fue precortada a la medida, preperforada en las ubicaciones de conexión y etiquetada de manera única. Las piezas se agruparon y todo el paquete de armazón cabía en un solo camión. En el lugar de trabajo, las piezas se ensamblaron en componentes de pared y armazón. Encajan como 'Tinker Toys'. No se requería medir ni marcar para ensamblar; solo para verificar dimensiones.
En el otoño de 2017, una pequeña empresa nueva en Sundance, Wyoming, intentó algo nuevo. La empresa se llama Straight Cold Rolling, LLC y querían construir un edificio estilo granero de postes de 60'x140' utilizando acero conformado en frío.
No había sierra en el sitio de trabajo (sin cortar), solo varias pistolas atornilladoras. Un equipo de cuatro trabajadores no capacitados fue instantáneamente productivo porque las piezas estaban perfectamente hechas.
¿Cómo hicieron esto? Utilizando el potente software SmartBuild, los planos estructurales se elaboraron en el software de diseño 3D. Las columnas y vigas de la pared se formaron en paneles. Las armaduras se diseñaron para un espacio libre de 60 pies. Se controló la geometría y el ajuste de cada panel de pared y armazón en el software. Luego, cada pieza de material se cargó en un archivo de datos que se introdujo en una maquinaria especial de perfilado. La máquina tomó bobinas de acero en bruto y las transformó en las piezas especificadas por el archivo de datos.
Los resultados fueron sorprendentes. El costo de las materias primas más la mano de obra de fabricación para formar rollos y empaquetar las piezas era competitivo con el costo de un edificio de madera equivalente. Esto fue inesperado porque el costo de los materiales de construcción de acero conformado en frío en otros segmentos del mercado generalmente supera el costo de los materiales de madera. Una sorpresa aún mayor surgió en los costos laborales de campo. Debido a que las piezas se fabricaron para encajar entre sí sin medir, marcar o cortar en el campo, un equipo no capacitado erigió el edificio tan rápido o más rápido que un equipo capacitado podría construir un granero de postes de madera.
Diseño de marcos
El edificio fue diseñado para albergar hasta cuatro espacios comerciales independientes. Las dimensiones del edificio eran de 60 pies por 140 pies y la pared sur incluía (4) puertas basculantes de 12 pies, cada una con una puerta de entrada adyacente. La altura de la pared era de 16 pies y la pendiente del techo era de 4:12. No había voladizos en el techo.
La solución de estructura incluía varias características para facilitar el proceso de construcción. Los paneles de pared se diseñaron en secciones de 4 pies. En un extremo del panel, el montante vertical (calibre 14) terminaba dentro del riel superior; en el otro extremo, el montante vertical (también de calibre 14) se extendía a través del riel superior 18 pulgadas adicionales. Cuando se colocaron dos paneles uno al lado del otro, los pernos de los extremos de calibre 14 se sujetaron en el campo formando una I. El montante corto se convirtió en el punto de apoyo para la armadura de arriba (también con una separación de 4 pies entre centros), y el montante largo proporcionó una conexión para la armadura (altura del tacón de 18 pulgadas) que también formó una conexión resistente a momentos para el marco del edificio.
Las correas del techo se fabricaron en longitudes de 12 pies. Los sistemas usaban formas cee para correas orientadas boca abajo y cada correa tenía muescas especiales cada 4 pies para recibir las armaduras. Esto creó un espaciador automático para colocar las vigas de forma rápida y precisa, aumentando la velocidad de montaje en campo.
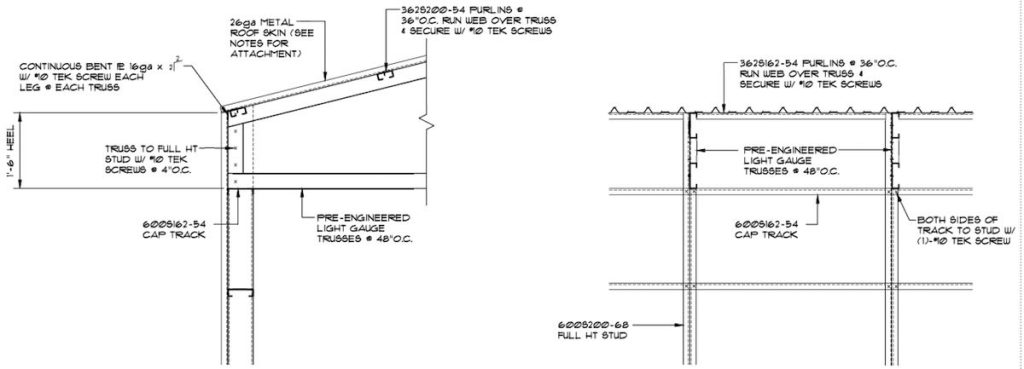
Ingeniería
La ingeniería estructural fue completada por Krivonen Associates en Billings, MT. El edificio fue diseñado bajo IBC2012 con una carga de nieve en el suelo de 30 psf y una velocidad máxima del viento de 120 mph. Se requirió un muro de corte interior para soportar el diafragma de 140' en la dirección transversal y se incluyeron los detalles de la conexión del diafragma.
El constructor deseaba un piso de concreto, por lo que esta base consistía en una losa de 4″ con cimientos de borde engrosado de 18″ de ancho x 24″ de profundidad usando (3) barras de refuerzo #4 en la parte superior e inferior. Los paneles de pared se sujetaron a los cimientos con anclajes de 5/8″ x 8″ a 32 ioc y se instalaron dispositivos de sujeción en las esquinas. Dado que no todos los edificios requieren un piso de concreto, actualmente se están investigando opciones de cimentación adicionales, como una base continua o tal vez un sistema de pilares de concreto sobre el que se apoyarían las columnas de la pared, ancladas con dispositivos de sujeción de acero.
Los trusses se diseñaron utilizando un potente software de diseño de trusses y un sistema de trusses patentado llamado KeyTruss que utiliza formas cee estándar con muescas especiales y marcado de piezas para facilitar la fabricación. Las armaduras estaban espaciadas 4 pies en el centro y debajo de cada armadura había una columna construida a partir de un montante cee adosado. Las cerchas se diseñaron con un espacio libre de 60 pies y una altura de tacón de 18 pulgadas para formar la conexión con el panel de pared. Las armaduras se diseñaron con bridas de 2 pulgadas, lo que eliminó la necesidad de cualquier arriostramiento de red. Las cuerdas de la armadura tenían formas cee de calibre 6 de 14″ (600S200-68) con muescas especiales en las bridas para recibir las redes en cada unión. Las redes de armazón tenían formas cee de 3 5/8″ y variaban entre calibre 18 y calibre 16 (362S200-54 y 362S200-43). Las correas de las armaduras se fabricaron con formas cee de calibre 3 de 5 8/16” (362S200-54) orientadas boca abajo con muescas para recibir las armaduras. Las correas se espaciaron a 36 pulgadas en el centro.
Las columnas se formaron uniendo dos cee de calibre 6 de 14″ (600S200-68) para formar una sección en I. Las columnas se espaciaron 4 pies en el centro para alinearse con las armaduras de arriba. También son posibles paneles de pared más anchos con espaciamientos de vigas más amplios. Los rieles superior e inferior de los paneles de pared se hicieron con formas de calibre 6 de 16″ (600T150-54) con hoyuelos que coincidían con las columnas verticales. Los hoyuelos permitieron que las pistas y las columnas se unieran incluso antes de desenroscar la conexión. Las viguetas de pared estaban hechas de formas cee de calibre 6 de 18″ (600S200-43) y tenían muescas especiales para quitar el alma y los labios por donde pasaban las columnas. Este detalle permitió un material fuerte que también podría recibir el revestimiento exterior así como el revestimiento interior. Las viguetas de pared estaban espaciadas a 24 pulgadas en el centro.
Lista de materiales
Los materiales fueron fabricados en Marion, Kansas. Se utilizó maquinaria especial de perfilado para convertir bobinas de acero en bruto en las piezas inteligentes que formaron el edificio. Cada palo para cada pared y armazón era una pieza altamente procesada con marcas y muescas personalizadas.
El peso de todos los materiales, incluidas las paredes, las vigas, las cuerdas y las redes de las armaduras, las correas del techo y el arriostramiento permanente sumó 42,000 lbs. Dado que las piezas se pueden agrupar de manera compacta, todo el trabajo cabía en un camión y el camión se pesaba y luego se enviaba al lugar de trabajo en Wyoming.
Construcción
Se entregaron paquetes de materiales al sitio donde la losa ya se había vertido y preparado. Todos los paneles de pared y cerchas se ensamblaron en el sitio.
Dado que todas las piezas se cortaron a la medida, se preperforaron con orificios guía y hoyuelos, y tenían marcas personalizadas, los componentes de la pared y la armadura se unieron como 'Tinker Toys'. Una cuadrilla de cuatro trabajadores que anteriormente no tenían experiencia en construcción de edificios, más un supervisor experimentado, ensamblaron rápidamente todas las paredes y vigas y erigieron el edificio.
No hubo necesidad de cortar en campo los componentes porque cada pieza había salido de la maquinaria precortada a la longitud exacta. El corte de campo solo fue necesario para abrazaderas de pared temporales, etc.
No se requería jigging para construir trusses. Los trusses se ajustaban automáticamente, usando orificios de alineación y muescas en las cuerdas para construir correctamente cada truss. Los miembros del equipo construyeron la primera armadura usando los orificios piloto y compararon las medidas con los planos de construcción. El equipo encuadró un extremo de la armadura y luego destornilló el resto de los sujetadores necesarios. Una vez que se confirmó la primera armadura, se usó como plantilla para otras armaduras, que primero se ensamblaron usando los orificios piloto y luego se atornillaron.

Comparación de costos
Los costos de materiales y los costos de mano de obra de campo se rastrearon durante todo el proceso. Se obtuvieron dos ofertas competitivas de los principales fabricantes de graneros de postes que utilizan estructuras de madera. Al comparar los costos del marco, así es como se acumulan los números. La solución de estructura de acero generó una combinación de mano de obra y materiales que es menor que la solución de madera.
Conclusión
Se diseñó y diseñó un edificio estilo granero de poste de 60'x140' utilizando una nueva metodología de construcción. El software de automatización avanzado para el diseño de edificios y la ingeniería de armazones, combinado con maquinaria especial de perfilado, creó un nuevo sistema de construcción que se combinó perfectamente en el campo, como un producto de Ikea. El costo combinado de los materiales y la mano de obra en el campo fue menor que el de un granero similar con estructura de madera.
[Nota del editor: Para obtener más información sobre la industria emergente de estructuras de acero conformado en frío, consulte nuestro noticia de primera página en la edición de octubre/noviembre de 2021 de Revista de perfilado.]