Por Kenneth P. Lambert, Jr.
Se cita al filósofo griego Heráclito de Éfeso por haber acuñado la frase "La única constante en la vida es el cambio". El cambio siempre está ocurriendo, lo queramos o no. En el ámbito de la fabricación, como en casi todas las facetas del mundo empresarial, nos esforzamos por adelantarnos a los cambios en los mercados, las condiciones económicas y otras fuerzas que escapan a nuestro control.
Sin embargo, existe una forma de control que podemos y debemos ejercer. Este es un cambio autodirigido para mejorar dentro de nuestras organizaciones. ¿Cómo provocamos y dirigimos un cambio positivo de manera deliberada y reflexiva? Hay un término que puede ser familiar para algunos profesionales de la fabricación: kaizen. Este término se basa en las palabras japonesas "kai" (cambio) y "zen" (para mejor), que dan como resultado "cambio para mejor", a veces interpretado como "mejora continua" o "trabajar todos los días hacia un estado ideal".
Naturalmente, este es el tipo de cambio que todos esperamos, pero el término “kaizen” es más que una ilusión. Ha llegado a significar “un enfoque sistemático para la mejora empresarial” y requiere liderazgo, compromiso y autodisciplina. Gemba Academy, una organización de capacitación enfocada en la mejora continua, afirma que es esencial que las organizaciones desarrollen una "cultura de kaizen" si esperan lograr el éxito a largo plazo en sus esfuerzos de mejora continua. En palabras del fundador del Instituto Kaizen, Masaaki Imai, “Mejora diaria. Todos mejoran. Mejora en todas partes.”
El concepto de kaizen surgió en los años posteriores a la Segunda Guerra Mundial cuando las fuerzas estadounidenses ayudaron en la reconstrucción de la industria japonesa. Dada la escasez de tiempo y recursos materiales, las mejoras inmediatas y drásticas no eran viables. En cambio, adoptaron un enfoque que enfatizaba el cambio continuo e incremental. Un elemento clave fue involucrar a la fuerza laboral existente, capitalizando el conocimiento práctico y de resolución de problemas que poseían esos trabajadores.
Había lecciones que aprender de este momento de la historia. ¿Puede una organización realizar mejoras significativas en sus operaciones, a pesar de tener recursos limitados? Toyota descubrió que la respuesta era un rotundo "¡Sí!" De hecho, la idea de kaizen se asoció estrechamente con el "Sistema de producción de Toyota", un conjunto de filosofías de gestión desarrolladas por Toyota para eliminar el desperdicio. Este conjunto de principios, que otorga gran valor al compromiso de las personas de toda la organización, está descrito por Jeffrey Liker en su libro "The Toyota Way: 14 Management Principles from the World's Greatest Manufacturer".
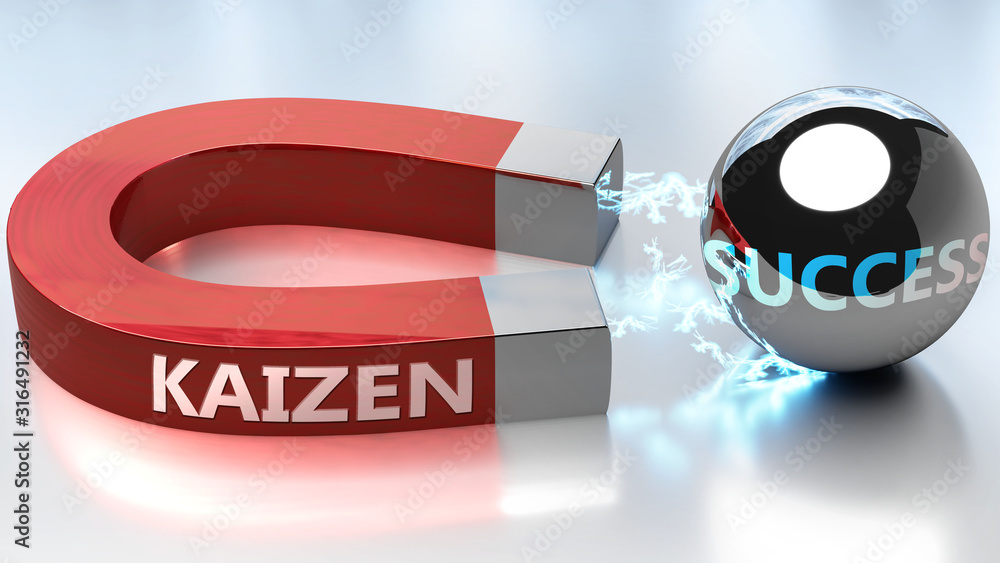
Jikoda
Una mentalidad que confía y espera que los empleados se conviertan en solucionadores de problemas seguros tiene aplicaciones concretas e inmediatas para el pequeño fabricante. El principio Toyota de jikoda — detener el proceso para corregir problemas — ilustra esta mentalidad. Jikoda no solo empodera, sino que de hecho requiere que los empleados detengan el proceso de producción en el momento en que vean un problema. El problema puede ser un defecto en una pieza o una desviación del estándar. Parece contrario a la intuición considerar el cierre de la producción como la clave para reducir el desperdicio. Sin embargo, si la producción continúa mientras se pasa por alto u oculta un problema, entonces el problema se agrava en forma de fallas, mantenimiento no programado, material desperdiciado o una reputación dañada. Alentar a los empleados a que detengan la producción cuando se detecta una falla produce recompensas a largo plazo. Evita que los defectos se vuelvan inherentes al producto final. También les da a los empleados un sentido de responsabilidad, comprometiéndolos verdaderamente en su actividad principal: entregar valor al cliente.
Heijunka
De manera similar, el concepto de Toyota de heijunka parece contrario a la intuición al principio. En un entorno en el que la entrega de productos justo a tiempo se considera el enfoque "esbelto" definitivo, heijunka sugiere que nivelar el volumen de producción y la combinación de productos es preferible a los cambios bruscos y reactivos en el flujo de producción. Los sistemas que reaccionan con fuerza a los picos y valles de la demanda tienden a provocar intervalos de infrautilización y sobreutilización de equipos y recursos humanos. Lo último que quiere un fabricante es un equipo inactivo, pero tampoco quiere que la falla de un equipo sobrecargado provoque paradas no planificadas. Las empresas que buscan crear una “cultura de kaizen” también deben minimizar las circunstancias que conducen a empleados demasiado estresados y desconectados que ya no buscan mejorar o llaman la atención sobre los defectos de producción. Un flujo de volumen moderado a veces puede requerir que los clientes esperen el producto, pero también protege contra las paradas no planificadas y las deficiencias de calidad no deseadas. Estos resultados agregan valor para sus clientes.
Evento Kaizen o Entrenamiento
Otra forma de ver kaizen es en forma de "evento kaizen" o "entrenamiento", un proceso de 1 a 5 días diseñado para capitalizar la experiencia práctica de los participantes. El Dr. Richard Chua, profesor y capacitador certificado en Lean Six Sigma, define un evento kaizen como un "evento bien organizado, estructurado y facilitado para mejorar un área de trabajo, un departamento, un proceso o un flujo de valor completo". Con una “cultura de kaizen” como base, un “evento” kaizen busca involucrar a las partes interesadas en toda la organización.
Un evento kaizen tiene sentido cuando es posible un análisis rápido del problema y se pueden realizar mejoras inmediatas utilizando herramientas simples, sin requerir un análisis de datos riguroso. Para aprovechar al máximo esta inversión de tiempo, se debe realizar un evento kaizen bajo la guía de un facilitador capacitado en herramientas de excelencia operativa. El facilitador guía el proceso para que se hagan las preguntas correctas y se aproveche bien el tiempo. En primer lugar, se debe definir el objetivo y el alcance del evento. Por ejemplo:
• Introducción de controles de calidad y rendición de cuentas en el proceso (Jikoda)
• Refinar el flujo de trabajo (como aplicar el principio de Heijunka)
• Identificar la causa raíz de un problema de calidad recurrente
• Optimización de la configuración del equipo
• Reorganización de un área de trabajo para mejorar la eficiencia.
No se puede enfatizar demasiado que tal evento depende de las personas. Es un ejercicio dirigido y centrado en las personas, por lo que se debe invitar a participar a las personas adecuadas. Esto incluye a los operadores, trabajadores de planta y otras partes interesadas que pueden brindar información única. Otros en el flujo de valor pueden aportar una variedad de perspectivas. Incluso los clientes pueden estar involucrados. Estas son las mismas personas que confían en el valor creado por el proceso en cuestión, por lo que su participación puede ser extraordinariamente poderosa.
Una vez que se define el resultado comercial deseado, se pueden emplear una variedad de técnicas de resolución de problemas. Por ejemplo:
• Mapear el flujo de partes o transacciones a lo largo de una instalación para comprender lo que realmente está sucediendo
• Un “Gemba Walk”: caminar por la planta de producción (Gemba = “el lugar donde se crea valor”)
• Análisis de procesos y valor agregado para determinar qué pasos agregan o no valor
• Desarrollo de diagramas de causa/efecto
• “5 por qué”: preguntar “por qué” una sucesión de 5 veces para descubrir la causa raíz de un problema
• Ejercicios de 5S para clasificar y organizar elementos, siguiendo la premisa de que todo tiene su sitio y cada cosa debe estar en su sitio.
Una vez que el evento haya concluido, los participantes deben emerger con una lista de recomendaciones para soluciones concretas y viables que se pueden poner en práctica de inmediato. Dado que son las propias partes interesadas quienes desarrollaron estas soluciones, normalmente hay un mayor grado de aceptación para la implementación.
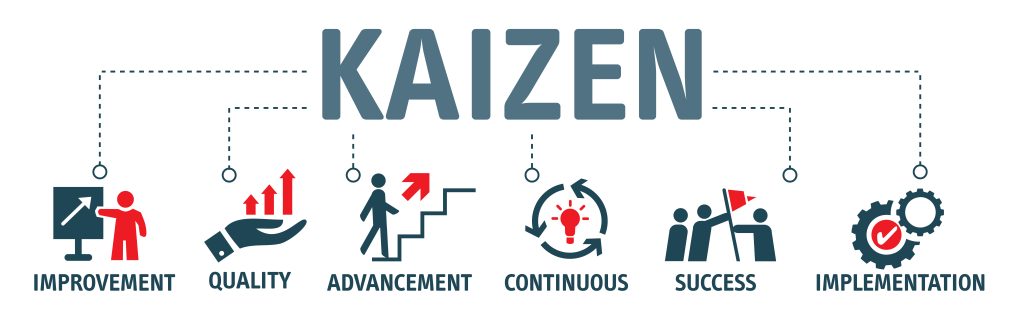
Poniendo “Mejora Continua”
En practica
Si bien los grandes fabricantes a menudo emplean expertos para liderar los esfuerzos de mejora continua, como los eventos kaizen, los fabricantes más pequeños a menudo no tienen experiencia en ese conjunto de disciplinas o la capacidad para contratar personal dedicado con ese conjunto de habilidades.
Afortunadamente, hay muchos recursos disponibles. Hay programas de capacitación, seminarios, series de videos y libros especializados en estas técnicas. Muchas universidades ofrecen extensiones de fabricación que brindan servicios de consultoría y capacitación de bajo costo a las empresas locales. Por supuesto, hay consultores calificados ansiosos por asociarse con fabricantes que están listos para comenzar su viaje de mejora continua.
Conclusión
Muchos de estos preceptos se pueden implementar de inmediato para generar efectos positivos, pero es útil considerar la mejora continua como un maratón. Comprometerse con un maratón requiere una mentalidad de maratón. Cualquiera que haya completado uno sabe que es una experiencia que cambia la vida. El arduo trabajo requerido para lograr ese objetivo a largo plazo finalmente demuestra su valor. De manera similar, hay más en kaizen que solo el evento kaizen o el "entrenamiento". Un entrenamiento kaizen es solo eso... un entrenamiento. Es bueno para ti. Dará soluciones prácticas a los problemas. Pero no es todo el maratón. Como explica un profesional de la mejora continua, los eventos kaizen resuelven problemas específicos, pero lo que es más importante, enseñan a los empleados a convertirse en solucionadores de problemas. Ayudan a fomentar la pasión por la mejora continua dentro de su equipo. Los equipos que participan en una "cultura de kaizen" se apropiarán de sus trabajos con la idea de crear valor para el cliente. De eso se trata: desarrollar una cultura en la que se confíe en las personas, todos en la organización, se les empodere y se les anime a desempeñar un papel activo en el cambio positivo. Todos están totalmente comprometidos en lograr un estado ideal: el máximo valor para el cliente. RF