Шэрон Тэтчер
Переход на конструкции из легкой стали – это непростое решение, но Тодд Тобер, владелец компании Tober Building Company в Ричфилде, штат Огайо, рад, что он это сделал. Его более традиционная строительная компания GC была основана восемь лет назад с двумя сотрудниками и сейчас является одной из пяти принадлежащих ему взаимосвязанных компаний, в которых работают 53 человека. Во многом его рост можно объяснить включением LGS/CFS в его список вариантов строительства.
РАННЯЯ КАРЬЕРА
Тобер начал свою карьеру в строительстве в качестве профсоюзного плотника. «Мой опыт связан с традиционными металлическими шипами», — отметил он.
В 2013 году он открыл собственную генподрядную и девелоперскую компанию, ориентированную в первую очередь на рынок многоквартирного жилья. «У нас все было хорошо, но всегда стоял вопрос, как сделать лучше», — сказал он.
У него была возможность отремонтировать модульное здание, строительство которого было завершено в 1980 году. Ему понравилась эта концепция, и он решил: «Давайте найдем способ построить модульное здание самостоятельно».
Сначала они экспериментировали с деревом. «Мы начали с дерева, и мне просто не нравилось качество продукта, который мы производили. Дерево есть дерево, оно сжимается, деформируется и трескается, и оно непостоянно, поэтому мы отказались от идеи с деревом и начали строить из стали», — сказал он.
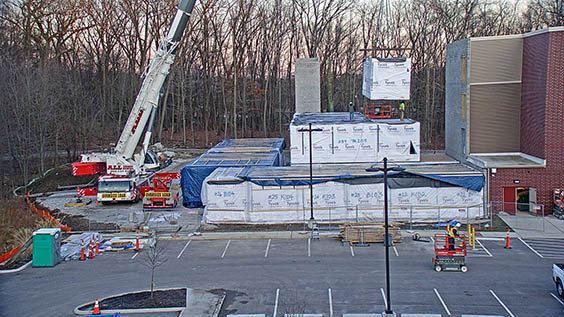
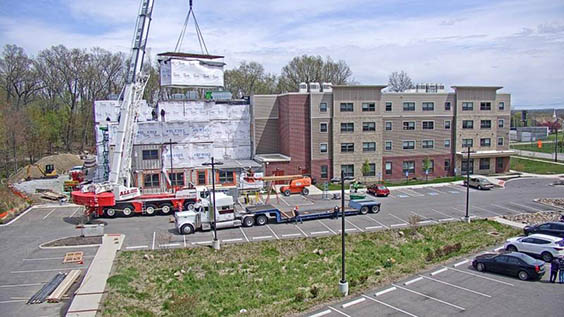
Модульные блоки ToVee устанавливаются на место краном. Их использовали для пристройки к существующему зданию.
ПУТЕШЕСТВИЕ К LGS/CFS НАЧИНАЕТСЯ
Встреча с Томом Ридом, торговым представителем Howick Ltd. в США, изменила правила игры. После обсуждений и бессонных ночей Тобер впоследствии приобрел две машины Howick для строительства новых модульных многоквартирных домов в рамках своего девелоперского бизнеса. Используя стандартное 3D-программное обеспечение REVIT, его медленно растущая компания смогла внедрить подробные планы в свое производство. Одна из машин производит металлические шпильки диаметром 3.162 дюйма в рулонах от 16 до 20 калибра; их более крупная машина Howick 7800, единственная в Северной Америке, производит пять профилей из металлических шпилек 6, 8, 10, 12 и 14 дюймов из рулона калибра 12–16.
«С помощью 3D-программы мы смогли создать файл станка с ЧПУ, который будет подаваться в профилегибочный станок для производства наших металлических стоек для установки в модульные жилые блоки», — описал он, добавив: «Это изготовленные на заказ стойки, с маркировкой, где встречаются гусеница и шипы. Соединения очень просты».
Но проекты развития Тобера не идут один за другим, и оставлять его профилегибочное оборудование бездействующим казалось не очень эффективным. «Итак, директор завода и я придумали способ получения дохода на заводе, пока мы ждали начала следующего модульного проекта», — сказал Тобер. Идея заключалась в том, чтобы предоставить материал для своих проектов генерального подряда.
Их первым тестовым случаем был проект по сохранению исторического наследия в Кантоне, штат Огайо, по превращению квартала и бетонного здания школы 1910 года в доступное жилье для престарелых. Здание, бездействовавшее около 20 лет, было выпотрошено, чтобы создать чистый лист. Новой дочерней компании Тобера, Atlas Framework, было поручено производить металлические шпильки. «Мы вышли и разложили все стены квартиры в 3D-программе», — описал он, а затем отправил то, что мы называем производственными пакетами — просто пачками стеновых панелей — на строительную площадку». Программное обеспечение было необходимо для определения того, как поступить со многими вариациями измерений стареющего здания, которые были созданы в результате многих лет выветривания, износа и оседания.
Когда началось строительство нового интерьера, успех каркаса LGS/CFS быстро стал очевиден. «То, что мы увидели, — это огромная экономия труда, потому что производство этого типа каркаса с нестандартными шипами происходит намного быстрее, чем обычно при традиционном каркасе с металлическими шипами», — сказал Тобер.
В отличие от традиционного металлического каркаса, который режется на месте, команда Тобера использовала систему LGS/CFS для предварительного измерения, предварительного выреза и предварительного сверления для размещения болтов. На строительной площадке детали просто крепились болтами, как монтажный набор. Скорость строительства уменьшила опасения по поводу цены на металл, поскольку одно уравновешивало другое.
Обучение строительной бригады, привыкшей к более традиционным строительным методам, не представляло большой проблемы, но потребовало участия бригады.
«Нам пришлось отправить на строительную площадку новую вещь и надеяться, что бригада, привыкшая делать все по-своему, примет новый процесс, — сказал Тобер, — и буквально в течение часа они поняли, как читать чертежи и как соединить вещи. Это была очень быстрая кривая обучения».
Он подсчитал цифры и обнаружил, что их метод строительства LGS/CFS на 400% быстрее, чем традиционный каркас.
ОДИН БИЗНЕС, ТЕПЕРЬ ПЯТЬ
Сегодня Тобер управляет пятью предприятиями: Tober Building Company, его генеральной подрядной компанией, которая работает в основном на северо-востоке Огайо; Tober Development Co., занимающаяся землеустройством; Тови, компания по производству модульных модулей, работающая в Огайо, Пенсильвании, Индиане и Мичигане, занимающаяся постройкой комплектных модулей, доставляемых на рабочие места; P&G Electric, коммерческая электротехническая компания; и Atlas Frameworks, производящие пакеты каркасов, которые можно доставлять куда угодно. На момент интервью пакеты каркасов Atlas использовались для проекта отеля в Канаде.

Фотографии предоставлены ToVee
ВЗГЛЯДЫ НА БУДУЩЕЕ LGS/CFS
Тобер является одним из множества подрядчиков по всей стране, использующих LGS/CFS, но считает, что это лишь вопрос привычки, которая мешает другим присоединиться к нему в том, что он считает прибыльным.
«Тяжело убедить людей измениться, — сказал он. «Любой, кто работает в сфере строительства, знает, что как только вы научитесь зарабатывать деньги с помощью определенного метода, вы не решитесь что-либо изменить… Они изобрели пневматический пистолет для забивания гвоздей, и людям потребовалось время, чтобы перейти от молотков к пистолетам для забивания гвоздей, но вы знаете, это не проблема, просто нужно время, чтобы измениться».
Он отдает должное своим сотрудникам за облегчение изменений. В прошлом году они продемонстрировали самый большой рост с добавлением 30 сотрудников. В штате шесть специалистов по моделированию BIM для разработки проектов.
«У нас очень, очень классная команда, — сказал Тобер. «Люди делают бизнес, и я думаю, что наши люди — лучшие в нашем деле. Они сделали процесс более плавным и упростили переход от одного метода строительства к другому».
Тобер также преодолел препятствия, чтобы получить сертификат ICC. «Это руководящий орган индустрии металлоконструкций, поэтому мы соблюдаем все их требования. Мы проходим через очень строгий процесс обеспечения качества, чтобы убедиться, что каждый отправляемый нами кусок стали соответствует стандартам, которые мы установили в нашем процессе сертификации».
Тобер сказал, что он по-прежнему использует древесину, но все чаще находит способы использовать LGS/CFS. «Я думаю, что задача состоит в том, чтобы выяснить, что работает, а что нет», — сказал он, добавив: «Название игры — быть креативными и гибкими, и это то, что мы пытаемся делать». РФ
СТАТЬИ ПО ТЕМЕ
Ожидается рост популярности LGS/CFS