By Sharon Thatcher
Chipley, Florida is a very small town (population 3,525) in the Florida Panhandle, but one of its businesses–Kent Construction and Roofing Inc. [kentconstructionandroofinginc.com ] serves a clientele that’s anything but small. Located in an area that has a concentration of military bases, the 30-year-old business has installed roofing on nearly every military base from Moody Air Force Base in Valdosta, Georgia, to Marshall Space Flight Center in Huntsville, Alabama, Keesler Air Force Base in Biloxi, Mississippi, as well as Naval Air Station Pensacola, Tyndall Air Force Base, and Eglin Air Force Base all in Florida. Because of their tri-state location their motto is “bringing the tri-states together under one roof”.
Residential is not in their wheelhouse, but federal and state projects, schools, and commercial are.
The History
Brian Kent, now president of the company, said his father Ronnie, the founder, saw the advantages of metal roofing and using a jobsite roll former long before his future competition. Established in 1980, Kent Construction started as a general contracting business but soon expanded to roofing.
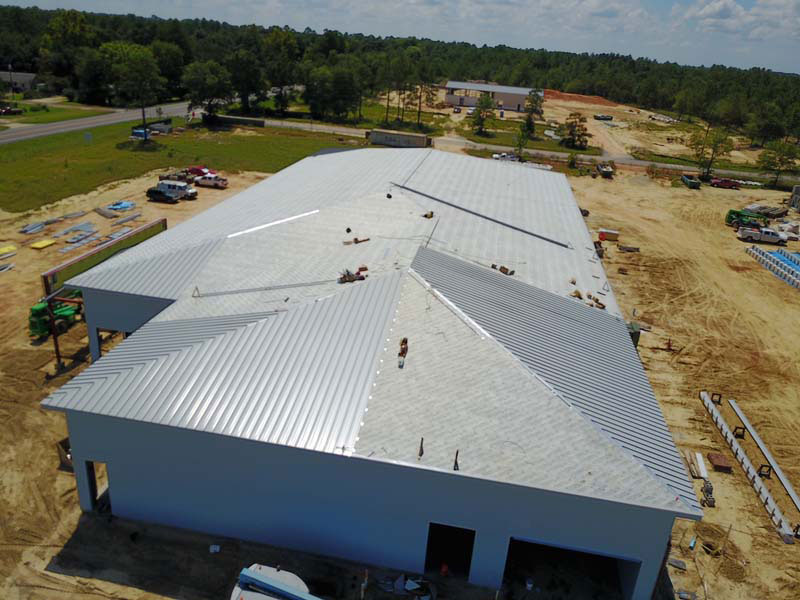
“At that time, in the Panhandle, there wasn’t a lot of construction going on and there were a couple other general contractors fighting over the same hand full of jobs,” Brian said. “Sometime in 1984 or 1985, a job came about that didn’t have a roofer on it. My dad said, ‘I think we can perform that ourselves.’”
It was a single-ply, modified sheet roof and the job went so well that the contractor asked if Ronnie would be interested in additional roofing jobs in South Florida. He sent one of his crew down to do the work “and it was three years later before he could come back,” Brian said, “he was doing so many roofing jobs.”
By the time he did come back it was the latter part of the 1980s and a new roofing trend had made its way to the Panhandle. “They had started to see a big influx of retrofit metal roofs,” Brian said. “We were in on the early stages of that. We had a stick-built metal frame system we’d build up from flat roofs on area schools and put standing seams on top.”
The company started with 10,000 sq. ft. projects and grew over time to projects well over 100,000 sq. ft. Their largest was a 220,000 sq. ft. school roof.
The “sweet spot”, Brian said, is 20,000-40,000 square foot roofs. “We can get in and out in two months. On new construction, like new schools or 160,000 square foot hangars, those jobs go on and on forever.”
In the earliest years, their panels were factory-formed by a large company and shipped in. “But you know how it is when you get to the end of a job and you’re a piece of trim or a panel short and you have to wait on those guys to do it, so we got our own machine. If we came up short, we could roll our own and finish the job. That’s how it all started,” Brian explained. It was 1989 and the machine was a Knudson KR 24 portable.
As the trajectory for metal roofing kept going, the company’s focus continued to shift. Today they focus solely on roofing; about 75% standing seam metal and 25% single-ply. The one Knudson was eventually joined by two more. A third portable is a New Tech. Two other machines serve the company, both from Roll Former Corporation: an RFC gutter machine and an RFC soffit machine. Only the soffit machine is shop-based. The portables are hauled on a flatbed pulled by a Ford F-650.
Brian came onboard full time after graduating from college in 1997. He had grown up in the business and said he had always planned to work for his dad. “That was my plan, to always come work for him,” he said. His brother, Brad, a structural engineer, was also with the company but later left to open BTK Engineering nearby. “He still does all our engineering,” Brian said.
Ronnie retired in 2005, leaving Brian as president of the company that was renamed to reflect the addition of roofing work.
Growing Competition
The company’s list of routine customers remains impressive, but so does the growing competition. “When we started running standing seam panels, we were the only ones that were running jobsite roll panels at that time,” Brian said. Now there are several.
Still, they have the experience with big jobs to keep them competitive. The bid process is familiar territory with all its tedious details and demands. They can easily navigate working in a tri-state area where Florida codes dictate in one area, Georgia codes in another, and Alabama in a third. Brian makes it sound easy: “Georgia and Alabama are a lot more lenient as far as wind speeds and designs. Other than that there’s not a lot of difference. You have closer clip [in Florida] to compensate for wind speed.”
The Florida code has become stricter since 2018. “They were not quite as strict as Miami-Dade until 2018 when we had Hurricane Michael come through,” Brian explained. “It tore up Tyndall Air Force Base, and a 50-60-mile swath… all the way up into Georgia. When that happened, they started implementing some of the Miami-Dade stuff here.”
Standing seam panel, 24 gauge, is the most common panel they roll, with some occasional 22 gauge.
Kent Construction and Roofing relies on three metal suppliers for coil: Englert, Drexel, and Petersen Aluminum. For fasteners they use Threaded Fastener, Triangle Fastener, and for insulation, Altas Insulation.
Recent Challenges
Unfortunately, the past year has proven to be very challenging in the very segments of the economy that built Kent Construction and Roofing. As Brian explained, public projects are bid and won a year or two in advance of the work. Price increases are built into the bid, but unexpected was the precipitous rise in prices for coil this past year-and-a-half, along with unexpected supply-chain bottlenecks. Once bid, there’s no guarantee that the customer will pay the extra expense.
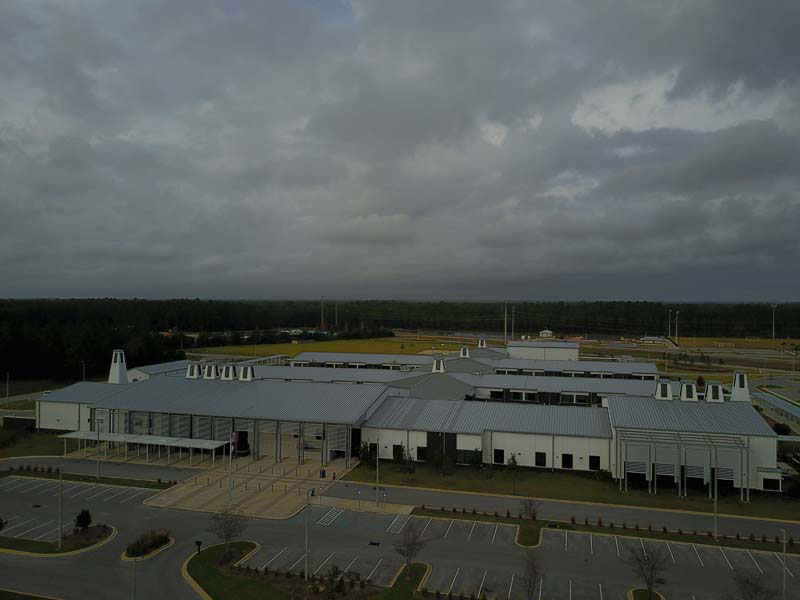
“My supplier will say, ‘I’m not going to supply you this coil stock at the price I bid you a year ago; your price is now twice that.’ …I’m having to pay that extra to get the product here because I contracted [with the owner to do the job a year ago]. Hopefully we’ll get to the point where the owner will pay it but we’re not to that point yet,” he said.
Getting to that point involves more time and paperwork. “We’re documenting the price [of supplies] of what we bid it and the price now and sending it to the government in an REA (Request for Equitable Adjustment). They’re supposed to take a look at it and give compensation, but there’s no guarantee that’s going to happen … I could possibly get burned, but it’s out of my control.”
While some prices are starting to moderate, aluminum, used along coastal areas, continues to go up. “In 2000, for example, we could buy 24-gauge coil stock for 68 cents a square foot. From 2000 to 2020, a 20-year span, it went up to $1.07. This past year, it has gone from $1.07 to increase, increase, increase, to where it is $2.16 right now. If you drew a graph for the last 20 years, you’d see 40 cents in 20 years, then jump $1.20 in a year. It’s unbelievable.”
Going forward, Brian said the company will need to anticipate greater price increases to build into their bids, “and if something happens where there isn’t a price increase, we can give some of that money back.”
But price increases are only part of the current headaches. On the supply side, foam insulation is not even available. “We can order it now for delivery a year out,” he said. “We are substituting XPS Polystyrene insulation. It is more readily available but twice the cost.”
Getting some coil colors has also been a challenge. “We used to be able to get any color in three or four weeks and now it’s taking three or four months.”
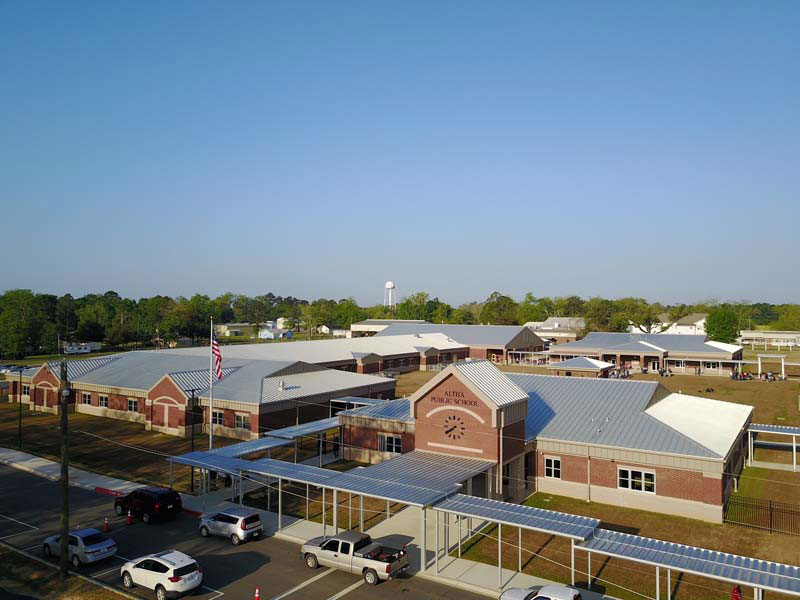
On new construction, the roof isn’t the first job to be tackled. Kent Construction often works with other contractors who are also facing supply chain issues, “so that pushes everyone behind schedule,” Brian said. “We’re lined up to do a job, and they’re not ready for us. It’s a snowball effect.”
And then there are the employee issues. Although Florida is seeing a large influx of newcomers, they don’t come inclined to work in roofing. “We have problems getting laborers,” he said, “but as far as the key people, we are blessed with a great team. We’ve had the same key people a long time.”
Sadly, one of those key people, Brian’s secretary, died unexpectedly late in 2021. “It was quite a blow,” he said.
“It seems like there’s always obstacles to overcome,” he went on to say, and at the end of the day the company has the time-tested experience to handle some of the toughest challenges head-on. As is often said in the office: “If it was easy, everybody would do it.” RF
Read more on this subject:
A Tale of Two Cities — Florida Style
Coastal Metal Roofing Sales
Emergence of Metal Helping to Change the Florida Landscape