By Karen Knapstein
Currently at $6.8 billion, the carport industry is a growing industry. Consumers recognize that choosing a metal-framed structure to store a vehicle, excess “stuff,” or even livestock is a near-instant solution to their storage problems. As a growing industry, it offers opportunity for roll formers.
A Growing Industry
Metal Rollforming Systems designs, manufactures, and builds panel lines, trim lines, and accessory pieces used in roll forming carport components, and other light gauge panels. Company President Bill Griffin reveals, “The carport industry as a whole continues to see record growth. This growth has placed a strain on existing component suppliers and manufacturers. This has caused many in the industry to bring manufacturing in-house as a way to reduce lead times, offset material cost incr. eases, and better control the quality of the products for their customers and crews.
Trending: Automation
“Like many industries,” Griffin continues, “the carport industry as a whole is seeing a shift towards increased automation. More and more carport manufacturers are transitioning from press brakes and folders to rollforming equipment. The exponential increase in speed helps to offset the ever-increasing labor costs and demands for their products. I believe the industry will continue to see growth in trim roll forming, and structural roll forming.”

Bending and folding trims with presses and press brakes takes a lot more time and labor than roll forming the components. When the labor cost is added to the material and facility costs, the price to make the components can outweigh the selling price. Automation yields higher throughput and production while simultaneously increasing accuracy. “Customers that roll form parts typically see a 10-20 fold increase in part production versus a traditional single folder or press brake manufacturing method,” explains Griffin. “They also benefit from more consistent part and angle measurements.”
Tube Forming
Ralph Girkins of Universal Tube & Rollform Equipment helps us explore the process of forming tube from coiled steel. Girkins, who has “made this business his business for 40 years,” founded Universal Tube & Rollform Equipment of Perrysburg, Ohio, in 1984. In 2005, he, along with Ken Metzger and Laura Smirin, formed Universal Controls Group (UCG) to offer their customers more options when buying metal-forming machinery. Today the company offers one of the largest in-stock metal-working machine inventories, machine reconditioning, on-site field services, new controls, drive systems, and buying and selling options for surplus machinery.
Girkins says, “We have 15 tube mills in stock and about 60 roll-forming machines, including used and rebuilt equipment. A lot of new guys want used equipment to get started. Once they start making money with it, then they want a new machine because they want to go faster. We can supply all the machines and equipment you need for a tube mill.” He says the typical cost for a new tube mill is about $600,000-$800,000, depending on the machines and tooling included in the lineup. A used machine is about half the investment.
Coil to Cut – How it’s Made
Odds are you are already rolling components used in building carports, since they are the same as those used in other metal buildings. Hat channel, commonly rolled from 26- and 29-gauge steel, is used to support roof and wall panels. U channel, used for braces and supports, help reinforce the structure. Panels and trims are rolled quickly and easily from 24-gauge to 28-gauge coil steel. Companies like ASC Machine Tool, Metal Rollforming Systems, and The Bradbury Company manufacture machines that roll form several profiles, eliminating the need for multiple trim machines.
Roll forming tube steel is a bit more complicated than roll forming panels and trims. The gauges used for carport framing are heavier — primarily 12- and 14-gauge steel. Tubing usually measures from 2” to 2 1/2”. “The gauge you use depends on the size of the structure you’re building. The bigger the structure, the heavier the gauge of framing you need to use,” explains Girkins.
There are more steps to the process and more equipment is involved in making steel tube. The high-speed equipment runs at a rate of 150-250 ft. per minute, although Girkins says they manufacture some mills that run at up to 1,000 ft. per minute.
There are several steps involved in turning a flat coil of steel into a round or square tube. If the tube will need holes or slots, they are punched into the steel before it’s formed into tube. Universal Controls Group manufactures machines that measure the flat coil steel and punch holes and slots in it. “It’s a lot easier to punch holes in the material while it’s still flat,” says Girkins.
The steel coils are butt welded to make a long, continuous strip and loaded onto an accumulator. Welding the butt ends together eliminates the need to re-thread the machine, it reduces waste and reduces changeover time between coils. It also reduces the risk of damaging the dies because of mis-threaded steel.
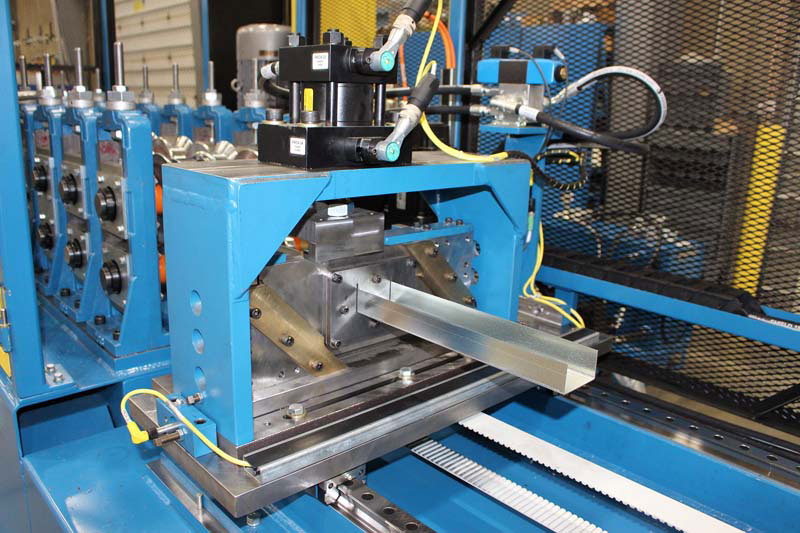
From the accumulator, the coil is fed into the mill into a pinch roll. “The mill never stops,” he explains. “The theory is you never shut the tube mill down. You use the accumulated material to keep it going until you’re done for the day.”
As the flat coil runs through the machine, it’s formed up and around until it makes a tube. It is like pulling the strip through a funnel. Before it’s cut, the tube goes through a high-frequency welder. “A high frequency weld isn’t welded with a torch,” Girkins clarifies. “The welder heats up the edges and the edges are squeezed together. It’s more forged than welded.”
The edges are heated up to approximately 1800 degrees, which is so hot the pre-galvanized protective zinc coating burns off the heated area and it creates an upset. A lathe tool is used to scarf off the upset material, making the area smooth again. A torch and automatic spray welder are used to reapply the protective zinc layer on the top of the seam.
After the zinc coating is reapplied, the round tube, runs through a 20’ cooling trough where it’s sprayed with coolant (water). The standard way to create the square tube used in framing carports is to make a round tube and then squeeze it into its square shape.
It usually takes three passes through the sizing mill to get the square shape. After it goes through the turkshead unit, where it’s straightened and squared (if desired), it runs through an encoder where it’s measured. Then it’ll go through either a flying saw or a cutoff. “Many carport people use flying cold saws now; it’s a nice, clean, easy way to cut,” he says. “There’s no deformation in tubing when the blade goes through and there’s no burr.” Neither the material nor the machine stop to make the cuts. A die travels along the tube at the same speed as the tube and makes the cut when it receives the signal from the encoder.
It’s at this point that the lengths are run through a swager, as a secondary operation, if needed. If the tube is going to be used for slip-fit construction, the lengths are put through a swager to squeeze one end of the tube enough that it will slip inside the end of another tube.
At this point, the framing components are finished and ready for your customer.
Conclusion
Tube mills are a major investment and they take up a lot of space; they may or may not be a good fit for your shop. However, if you’re ready to invest in a mill of your own to venture into supplying this growing market, there are plenty of companies that are ready to guide you. RF