By Sharon Thatcher
A forklift is likely one of the smallest and least expensive pieces of equipment you own yet you probably don’t pay much attention to it until it doesn’t work, or it hits an object like the side of your shop. But a forklift holds up its share of the workload, and you shouldn’t be so readily dismissive when it comes time to replace it, or to add to your existing forklift fleet.
There are many popular brands of forklifts, but MH Equipment, a dealer headquartered in Peoria, Illinois, cautions against buying a generic “out of the box” machine. Why compromise when the world of forklifts is quite extensive, with new models being introduced to handle nearly any situation?
MH, in the business of selling material handling equipment since 1952, is a regional (Midwest and East) dealer of multiple brands of forklifts, particularly Hyster and Yale. They also carry other specialty material-handling machines. Its material handling experts outline some of the major points you should explore when purchasing new.
Primary Use
The first thing to consider, MH notes, is an examination of how you plan to use your forklift. If it’s a replacement for an existing machine, and you are happy with how it performs and how it fits into your overall production, the decision is simple. But if your production or shop floor needs have changed, you may want to consider switching up to one that affords more flexibility and efficiency.
“Have a clear idea in mind about your ultimate interest in acquiring a new fork truck, so that equipment vendors can best match you to a suitable truck without over- or under-shooting your objectives,” the experts say.
MH cautions against making a hasty decision based only on availability. “In today’s volatile market, acquiring nearly any capital equipment piece and its necessary components calls for sometimes lengthy lead times, which may in turn drive you to making concessions on desired features or brands just to take delivery of an alternative selection in a reasonable timeframe,” they say, adding, “choose partners based on their ability to service your ongoing needs.”
If you need something in the short-term, a good partner will be able to help you.
While you are shopping around, there are some additional factors to keep in mind when speaking to vendors. MH lists these:
Type of Working Environment
A lift truck needs to be compatible with the surface type, exposure to weather, presence of dust and debris, and other environmental variables. Most directly, working environments determine a lift’s tire types. A solid cushion tire performs well on smooth indoor concrete surfaces, and a pneumatic tire works best for rough outdoor terrain.
In the roll-forming world, the pneumatic route is typically chosen because forklifts are often called upon to work a myriad of jobs both indoors and outdoors.
Capacity
For rollformers, an important topic will be a discussion on what capacity lift will meet your needs. Capacity for a fork truck means several things all at once:
• Weight of objects to be lifted
• Size, shape, and form of objects to be lifted
• Orientation and dexterity of lift needed to pick objects
• Any special requirements to lift objects safely and properly.
“This information leads us to both a base forklift chassis selection as well as several necessary accessories, such as a side-load turret with reach extension,” MH experts note. Additionally, you need to be able to provide information to the vendor on aisle width, rack height, sitting vs. standing operator, and load type (pallets, boxes, free-form products, etc).
Powertrain
Forklifts in the U.S. are primarily powered by electric, propane, or diesel. OSHA classifies them into seven general categories:
□ Class I: Electric motor rider trucks
□ Class II: Electric motor narrow aisle trucks
□ Class III: Electric motor hand trucks or hand/rider trucks
□ Class IV: Internal combustion engine trucks (solid/cushion tires)
□ Class V: Internal combustion engine trucks (pneumatic tires)
□ Class VI: Electric and internal combustion engine tractors
□ Class VII: Rough terrain forklift trucks
Electric lift powerplants are more efficient and exhaust no hazardous gases into closed warehouse spaces, but they usually have lower capacity and drive time durations in that they must be plugged in often to charge (usually daily). Internal combustion powerplants are more powerful, with higher work capacities and the ability to run continuously (as long as they have fuel in the tank), but are noisy, physically larger, polluting, and cost more to operate (given today’s fuel costs).
Duty Cycle
Duty cycle simply means how often the lift needs to be in use versus how long it will sit unused in a given time period. For example, a warehouse with a single shift may utilize their fork truck 8 hours on, 16 hours off, in a 24-hour day, which results in a duty cycle of (8/24) = 33.3%. This conveys a few key details about sizing the forklift. First, it won’t be used too extensively, and so can be selected from economical to mid-range feature tiers, keeping costs proportional to utilization. Second, the lift’s powertrain will consume fuel for 8 hours and then have 16 hours to refill, which is most applicable to battery recharge rates in electric lifts, but also is used to determine fuel tank sizes in combustion engine lifts, both solving for fueling a full work shift without stopping to recharge or refill. Third, duty cycles bear directly on operating costs, explained below.
Budget – Capital Expenditures and Operating Expenditures
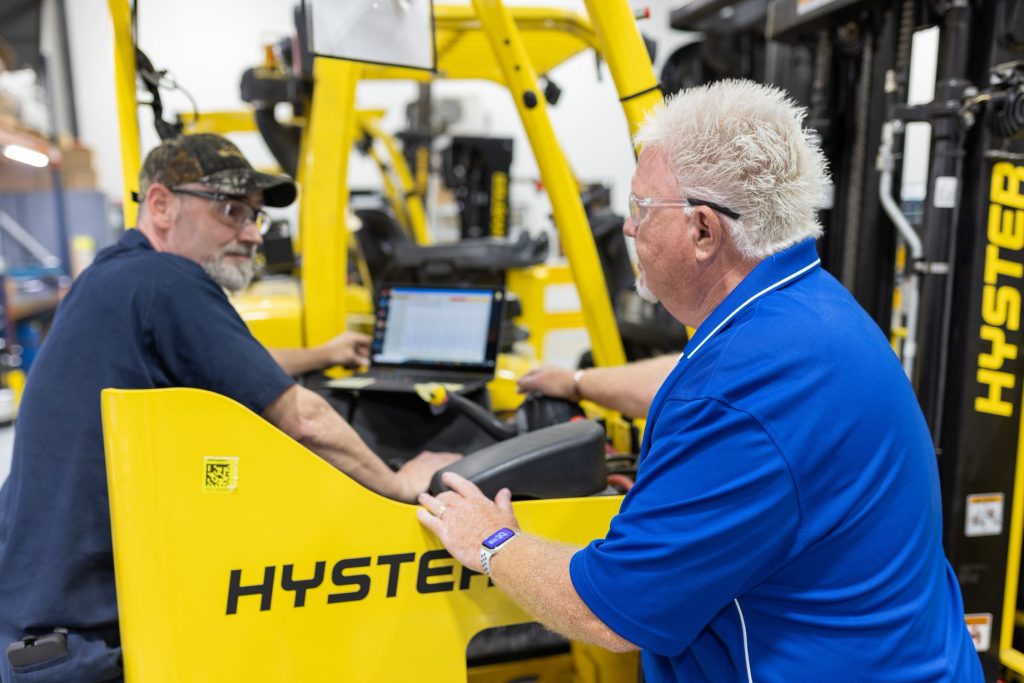
MH warns not to forget factoring into your purchase budget the long-term and cost-benefit elements that also have cost implications. Consider establishing your budget with three items in mind:
Initial Purchase Cost: You’ll want to know your company’s available capital purchase allowance and compare that against multiple fork truck manufacturers and vendors to gain a sense of the current going rate of trucks that meet your needs. Consider tax incentives, financing options, down payment requirements, state/government incentives (available in many forms such as energy conservation, industrial business growth, depreciating outdating / polluting assets, etc.) and vendor discounts.
Ongoing Maintenance Costs: Whether performed by internal or external teams, maintenance costs often exceed the initial cost of the vehicle given enough time, so these warrant close examination. Internal maintenance is usually more proactive and lower cost, especially when spare parts and consumables are kept in-stock. External maintenance can be more expensive per service call, but can bring greater value using the advanced tooling, knowledge, and experience available with professional service teams. In some cases, vendors can couple maintenance costs into service contracts bundled with the purchase price, alleviating complication especially for smaller businesses.
Emergency and Replacement Costs: Buying a very low-priced fork truck from a foreign distributor may save money initially, but if that unit has no local support and no domestic part vendors, the cost of downtime (especially emergency outages) can suddenly exceed the initial savings by a lot. Purchasing a fork truck should include considering emergency cost as well as future end-of-life replacement costs, both as a function of local vendor support and the OEM’s direct options. Some OEMs will buy back lifts for remanufacturing and resale at a reduced price, and some vendors will take old lifts as trade-ins towards new lifts.
Secondary Benefits or Features
MH Equipment’s material handling experts also encourage you to consider what secondary benefits or features you may need. “Do you need to haul the lift from location to location, requiring tie-down hooks on the lift? Do you need the ability to integrate telematics or other onboard technology? Do you need to swap accessories and attachments? Consider all future or secondary uses required out of the lift to make sure you’re not missing any critical functionality in a new fork truck,” they note.
Licensing and Safety Requirements
Depending on the locale, different lift classifications have different licensing and safety requirements that businesses must comply with. In most cases, forklift operators certified in one lift classification are not allowed to jump onto other classifications without completing certification on that lift class as well, even when the second lift appears ‘smaller’ or ‘less complicated’. Look into specific OSHA or other agency requirements applicable in your area for both licensing/certification as well as those governing written safety program.
Insurance
Forklifts often require insurance coverage which will bring along their own costs needing examination. Just like automobiles, lifts with newer safety features may often cost less to insure than older lifts, and costs may be further offset by additional training, management assets such as telematics systems, and overall low business incident ratings. Forklifts are not necessarily covered under a business automobile insurance plan, and also may be factored differently between owning and renting the lift. Be sure to check your coverage to make sure you’re properly insured.
Tips for Buying a Used Forklift
Forklifts can lead hard lives and while lifespans range from 5 to 15 years or 10,000 to 20,000 hours depending on the application, buying a used machine could mean buying more problems than solutions. A refurbished machine from a reputable dealer allows you to have someone to fall back on if something fails. No matter the source, however, here are some tips on what to ask when considering a used machine:
□ Ask for a history of the truck and the number of hours on the unit. The maintenance records should include scheduled changes of filters and fluids along with repairs.
□ Why is the machine being sold?
□ Check the tire tread. A line on the tire shows when a tire is worn out. When it reaches this point the tire needs to be replaced.
□ Check the hoses, including those located within the mast.
□ Check the chains for tightness. Chains can seize if not lubricated properly.
□ Check the heel of the forks. The bottom and the back of the forks should have a similar or same measurement. A disproportionate measurement can result in balance issues.
□ Check the bushing. Too much play can indicate excessive wear.
□ The overhead guard should be fully intact and inspected for damage. While forklifts do typically get damaged, it should only be cosmetic. There should be nothing bent or cut off that might pose a safety hazard. Having a hole drilled into the forks (often done to help move objects) is not an acceptable alteration under OSHA rules.
□ Drive it and check for any strange noises that might indicate engine problems.
□ Does it look like it has been cared for or neglected? Has it been painted to perhaps cover up problems?
□ What kind of work has it been put through, outdoors and indoors?
Toyota, which produces a popular forklift, says it’s time to consider replacing your forklift if you need one of the following repairs, so don’t compound your headaches by buying a worn-out machine that has one of these problems from the get-go:
• Hydraulic leaks
• Clogged fluid lines
• Worn chains
• A mast that won’t lift
• Battery problems
• Unbalanced suspension
• Steering difficulties. RF
Sharon Thatcher is the former managing editor of Rollforming Magazine. She is now an independent writer living in Ohio.
Coil-handling is Key to Efficiency (Further Reading)
If you’re going to spend millions of dollars on a roll-forming plant, but the tool you’re using to move materials within your operation has not been seriously considered, then you’re not going to maximize your investment. Those words of wisdom are offered by Paul Short, North American President for Combilift, world’s largest multidirectional forklift manufacturer. Combilift was founded in 1998 by Robert Moffett, inventor of the Moffett forklift, and Martin McVicar, the former head of R&D at Moffett. Their machines have found a niche in the roll-forming and lumber industries due to their ability to handle long loads in the direction of travel to help maximize space and safety no matter what length product. “We’re usually the last piece of the puzzle that anyone thinks of,” Short continued, but in reality, “to make a small investment in that piece of equipment could maximize your plant’s efficiency. Consultation with the material handling expects could offer great insights and gains for your business.” Combilift likes being able to travel to a customer’s shop site to investigate conditions and help make good decisions. “We can go visit the site, survey the materials, survey the loads, survey the application, all the conditions, and then help the customer by making a recommendation on the correct truck for them,” he said. “That’s part of our service rather than have the customer work that all out themselves. If space is a consideration, Combilift models integrate the counterweight into the truck chassis, maximizing maneuverability and allowing longer materials to be carried through narrower spaces. A conventional forklift is less adaptable to space issues because the counterweight is built into the rear of the machine, altering the triangle of stability. In addition to all the usual advice on knowing the kinds of loads and space restrictions your equipment will need to operate within, Short added this precaution: “Know the weight of 80% of your loads,” then consider the inevitable outliers. Popular Combilift options for rollformers include hydraulic fork positioner that allows the operator to spread or narrow the forks with the push of lever, and detachable spreader bars for wider spreads on longer loads. Combilift is headquartered in Ireland but has 300 service centers and 100 dealers in North America. |