Von Manfred Binder, Vertriebsleiter, Inline-Farbmessung, X-Rite
Beschichtete Stahl- und Aluminiumplatten sind ein wesentlicher Bestandteil der Bauindustrie, der Rohstoffindustrie und anderer Anwendungen. Da sich die Designtrends hin zu kundenspezifischen Farbarbeiten mit faszinierenden neuen Farben ausweiten, müssen Hersteller beim ersten Durchgang Genauigkeit und Wiederholbarkeit sicherstellen. Die Farbe muss an der gesamten Fassade und von einem Produkt zum anderen konstant sein.
Farbe ist so zum primären Qualitätskriterium geworden. Wenn die Farbe nicht einheitlich ist, ist sie leicht zu erkennen. Wenn eine Platte auf einem Dach oder Gebäude einen anderen Farbton hat, fällt das sofort auf. Wenn die Farbe nicht einheitlich ist, müssen die Produkte überarbeitet, verschrottet oder mit einem Preisnachlass verkauft werden. Dies wirkt sich nicht nur auf das Endergebnis eines Herstellers aus, sondern kann auch erhebliche Auswirkungen auf die Nachhaltigkeitsbemühungen haben.
Bei der Bandbeschichtung besteht die Herausforderung darin, Farbabweichungen frühzeitig in der Fertigung zu erkennen. Dies ist jedoch für Fertigungsprozesse nicht einfach. Aufgrund der hohen Produktionsgeschwindigkeit können sich die Bediener nicht an die genaue Farbe erinnern oder sie identifizieren, die vom Band kommt. Wird ein Coil hergestellt, hat der Bediener keine Chance, während des Prozesses Farbveränderungen zu erkennen, da diese langsam verblassen. Der Bediener kann Farbunterschiede nur dann erkennen, wenn die Muster nebeneinander liegen, als wären sie an der Fassade montiert.
Glücklicherweise können Fortschritte in der Farbmesstechnik Herstellern von Coil-Beschichtungen dabei helfen, Farbabweichungen sofort zu erkennen und teuren Abfall zu vermeiden.
Messen in einem Labor
Farbmessgeräte messen die Farbe unabhängig von Lichtverhältnissen und menschlichem Urteilsvermögen. Die Farbmessung ist zum Standard für alle Labore geworden, da sie zuverlässige Daten für die Eingangskontrolle der Rohmaterialien sowie die Endkontrolle der produzierten Coils liefert. Alle Daten werden gespeichert und sind somit nachvollziehbar. Das Labor ist eine wichtige Instanz, wenn Farbentscheidungen getroffen werden müssen. Hier formulieren und definieren Hersteller die Farbstandards für Coil-Coating. Diese Fachleute müssen Fragen beantworten wie: „Können wir dieses Produkt in der angegebenen Farbe versenden?“ oder „Haben wir die gleiche Farbe wie im letzten Monat oder im letzten Jahr geliefert?“ oder „Ist unsere Farbe bei jedem Durchlauf konsistent?“
Aber wie helfen diese Informationen dem Bediener beim Betrieb seiner Maschine? Sehr wenig! Er stellt eine Spule her, die am Ende aufgerollt wird. Nach Fertigstellung einer Spule wird eine Probe entnommen und ins Labor gebracht. Erst dann erhält der Bediener das Ergebnis darüber, was produziert wurde. Es ist, als würde man mit geschlossenen Augen ein Auto fahren und nur ab und zu einen Blick auf die Straße werfen, um die Richtung zu korrigieren. Niemand würde das tun, weil es zu gefährlich ist. Warum sollten wir das also auf der Beschichtungsmaschine tun?
Wenn es um Qualitätskontrolle geht, gibt es ein beliebtes Sprichwort: „Man kann nur kontrollieren, was man misst.“ Wenn die Farbe für ein Produkt wichtig ist, muss sie an der Produktionsmaschine gemessen werden, damit der Bediener die richtigen Anpassungen vornehmen kann, bevor die Farbe außerhalb der Spezifikation liegt.
Produktionsumgebungen erfordern eine Inline-Farbmessung
Die Messung von Farben in einem Labor unterscheidet sich stark von der Messung in einer Produktionshalle. In einem Labor befindet sich das Spektrophotometer in einer sauberen und gleichmäßigen Umgebung. Die Temperatur und Beleuchtung sind konstant und es gibt sehr wenig Staub. Die Probe wird auf Raumtemperatur abgekühlt und kann zur einfachen Messwertablesung direkt auf das Spektralphotometer gelegt werden.
Auf der Produktionsmaschine sieht das Szenario jedoch völlig anders aus. Bei der produktionsbegleitenden Messung ist Folgendes zu beachten:
• Messungen müssen berührungslos durchgeführt werden, damit das Spulenband nicht beschädigt oder zerkratzt wird.
• Die Messungen können nicht durch das normale Flackern und Umgebungslicht in der Produktionshalle beeinflusst werden.
• Die Temperatur des Raumes und des Spulenbandes können Farbmessungen beeinflussen. Bei der Messung einer heißen Spule müssen auch die Farbwerte bei Raumtemperatur berücksichtigt werden.
• Messungen an der Linie müssen genauso präzise sein wie im Labor.
• Die Produktionslinie bewegt sich schnell.
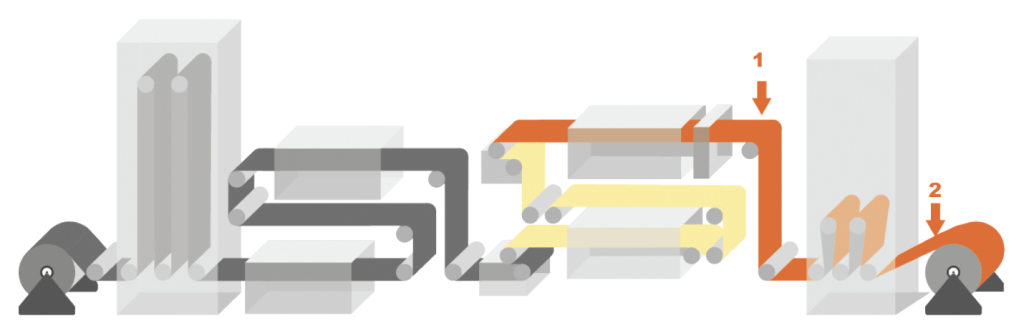
Die Farbmessung während der Spulenproduktion ist keine leichte Aufgabe. Glücklicherweise machen Fortschritte bei der Inline-Farbmessung und -Software die Steuerung und Überwachung der Farbe während der Bandbeschichtung einfacher denn je.
Heutige Inline-Spektralfotometer sind auf einem Querbalken montiert, um während der Produktion berührungslos die Farbe in Querrichtung zu messen. Mit diesen Informationen kann der Anlagenbetreiber die Nip-Presse der Beschichtungslinie steuern und der Farbküchenbetreiber kann sehen, wie sich die Farbe an der Maschine entwickelt. Wenn die Farbe zu driften beginnt, können sofort Maßnahmen ergriffen werden, um die Farbe innerhalb der angegebenen Grenzen zu halten.
Wo zu messen
Wenn Sie die Inline-Farbmessung zum Produktionsprozess hinzufügen, gibt es zwei Stellen, an denen die Farbe gemessen werden kann:
1. Direkt nach der Wasserabschreckung nach der Endbeschichtung. Durch die Platzierung eines Inline-Instruments werden Farbinformationen frühzeitig im Herstellungsprozess erfasst, um vorherzusagen, wie die Farbe aussehen wird. Ein Nachteil besteht darin, dass die Spule noch heiß ist und die Farbmesswerte auf Raumtemperatur umgerechnet werden müssen. Für die Durchführung dieser Berechnungen kann jedoch QC-Software verwendet werden, um eine hervorragende Korrelation zum Laborsystem zu gewährleisten. Dies wird im Abschnitt „Thermochromie“ weiter unten erläutert.
2. Nach dem letzten Akku. Hier ist die Temperatur kühler, aber leider nicht stabil. Abhängig von der Position des Speichers kann sich die Temperatur ändern, daher ist eine Thermochromie-Kontrolle erforderlich. Ein weiterer Nachteil besteht darin, dass die Geschwindigkeit des Bandes nicht konstant ist. Auf die Qualität der Farbmessung hat es keinen Einfluss, allerdings sind die Messpunkte auf dem Streifen nicht gleichmäßig verteilt, da der traversierende Strahl eine konstante Geschwindigkeit hat.
Insgesamt sind die Vorteile für die Farbmessung nach der Wasserabschreckung höher. Wenn möglich, wird empfohlen, die Messung nach der Wasserabschreckung durchzuführen. Eine Messung nach dem Akkumulator sollte nur dann in Betracht gezogen werden, wenn davor kein Platz zur Verfügung steht.
Thermochromie:
So vergleichen Sie die heiße Spule mit dem Labor
Bei der Coil-Beschichtung sind Produktspezifikationen und Farbtoleranzen oft sehr eng. Leider kann sich die Farbe mit der Temperatur ändern. Dies ist ein reversibler Prozess und wird Thermochromie genannt. Beispielsweise können die Farben Rot, Orange und Gelb bei höheren Temperaturen dunkler und weniger gesättigt erscheinen.
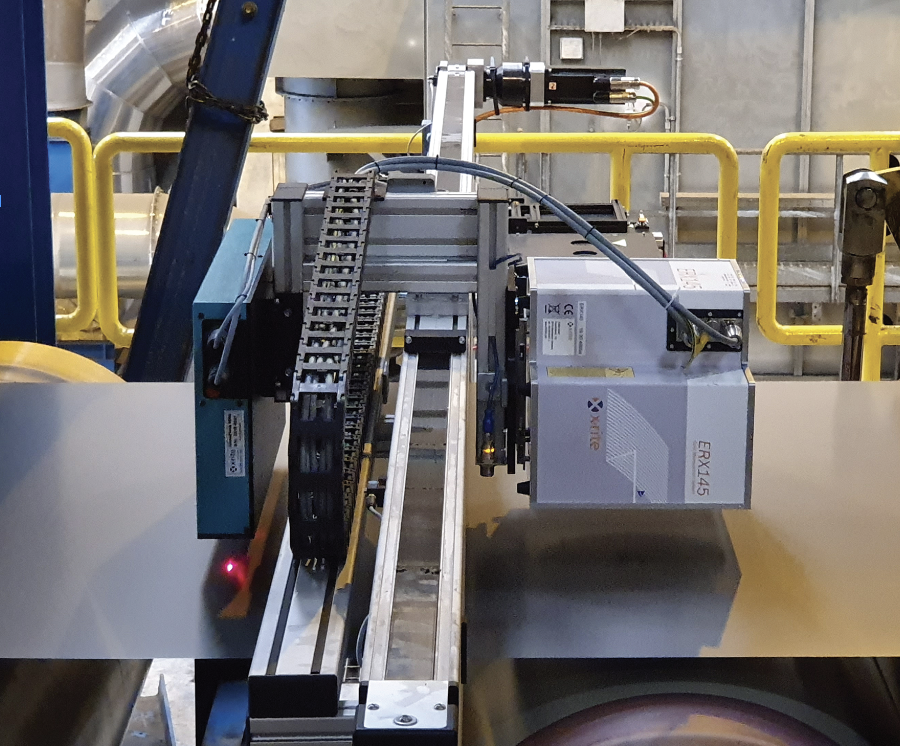
Auf der Produktionsmaschine wird die Beschichtung in einem Ofen ausgehärtet. Nach dem Verlassen des Ofens ist der Streifen ziemlich heiß. Selbst die Wasserabschreckung bringt das Band nicht auf Raumtemperatur. Wenn hier die Inline-Farbmessung durchgeführt wird, müssen wir diese Farbverschiebung berücksichtigen und die Messwerte auf Raumtemperatur umrechnen.
Inline-Geräte wie der X-Rite ERX145 verfügen über ein eingebautes Pyrometer, um die aktuelle Temperatur der Spule direkt am Messpunkt zu messen. Die X-Rite ESWin QC-Software empfängt die Farbwerte mit der tatsächlichen Temperatur und berechnet die Werte wieder auf die Raumtemperatur zurück. Auch wenn sich die Temperatur der Spule ändert, sind die Messwerte konstant und entsprechen der Messung im Labor bei Raumtemperatur.
Um den thermochromen Effekt zu spezifizieren, wird dasselbe Gerät für den Einsatz im Labor auf einem Heiz- und Kühltisch montiert. Jede Probe wird bei unterschiedlichen Temperaturen gemessen, um die Farbverschiebung zu kalibrieren. Die im Labor gemessenen Werte werden direkt an die Produktionsmaschine übertragen und als Standard verwendet. Dies erfordert, dass alle Instrumente eine hervorragende Übereinstimmung zwischen den Instrumenten und eine langfristige Stabilität aufweisen.
Eigenständig oder vollständig Integriert in das Produktionssystem
Inline-Systeme können als eigenständiges Gerät arbeiten oder vollständig in das Prozessleitsystem (PCS) integriert werden. In diesem Fall ist das Farbmessgerät ohne Bedienereingriff vollautomatisch. Sobald eine neue Produktion startet, wird das Target an den Farbsensor übergeben und die Inline-Messung startet.
5 Schritte zur Farbkontrolle bei der Coil-Beschichtung
Die Verwendung von Farbmessungen im Labor, an der Produktionslinie und in der gesamten abschließenden Qualitätskontrollberichterstattung hilft Herstellern, schneller und einfacher konsistente Farben zu erzielen. Hier sind die fünf Schritte, denen erfolgreiche Coil-Coater folgen.
Im Labor hilft ein auf einem Heiztisch montiertes Laborspektrophotometer dem Farben- und Lacklieferanten bei der Formulierung und Definition der Farbstandards. Der Standard wird unter Verwendung eines Heizsystems gemessen, um zu zeigen, wie sich Temperaturänderungen auf die Farbe auswirken.
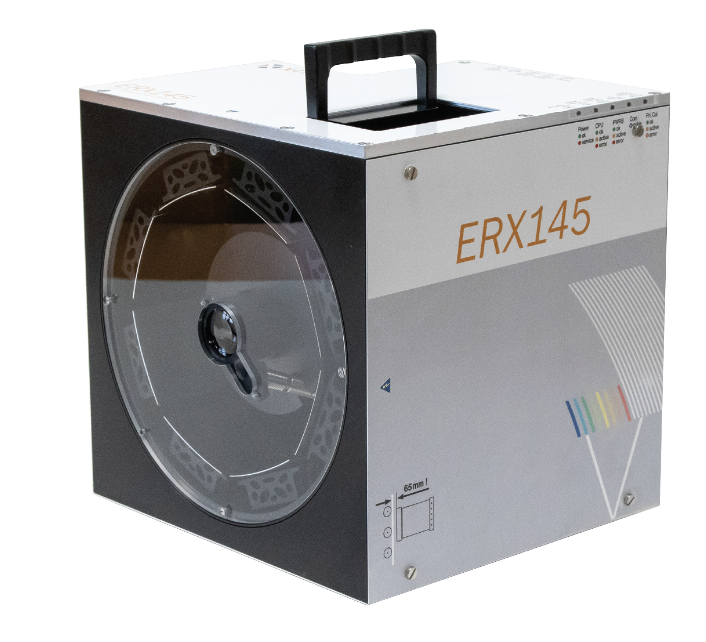
Nachdem der Farbstandard festgelegt wurde, wird er an alle am Arbeitsablauf Beteiligten weitergegeben, einschließlich des Lieferanten, der Arbeitsstationen in der Produktionskontrollkabine, an der Farbbeschichtungslinie und an den Kundenstandorten, sodass jeder Benutzer Zugriff auf dieselben Farbdaten hat.
Sobald der Coil-Coating-Prozess beginnt, bewerten Inline-Farbmesssysteme kontinuierlich die Farbqualität über die gesamte Länge und Breite jedes Coils. Der Querbalken hält und bewegt das Inline-Spektrophotometer in Querrichtung, sodass es messen kann, während sich die Spule bewegt.
Die Ergebnisse werden in Echtzeit geteilt, sodass jeder im Netzwerk die Farbqualität und -konsistenz überwachen kann. Wenn eine Farbtoleranz überschritten wird, machen Grafiken und Warnmeldungen alle darauf aufmerksam, bevor Farbabweichungen zu einem kostspieligen Fehler werden.
Das Inline-Farbmesssystem bietet eine vollständige Dokumentation in Form von Farbqualitätsaufzeichnungen auf der Grundlage internationaler Standards, um die Integrität des Programms und die Kundenzufriedenheit sicherzustellen.
Zusammenfassung
In einem modernen Produktionsprozess müssen alle wichtigen Parameter gemessen und gesteuert werden. Die Farbe ist einer der wichtigsten Parameter, da jeder einen Unterschied am Produkt bemerken wird. Während eine Messung im Labor notwendig ist, kommt die Information für den Maschinenbediener zu spät. Nur Inline-Farbmessungen können Bedienern dabei helfen, Farbverschiebungen früh genug zu erkennen, um die Beschichtungsmaschine anzupassen und qualitativ hochwertige, konsistente Farben zu erzeugen.
Das Hinzufügen einer Inline-Farbmessung zum Bandbeschichtungsprozess hat einen typischen Return on Investment (ROI) von sechs Monaten. Durch automatisierte Echtzeitmessungen während der Produktion verbringen Unternehmen weniger Zeit mit der manuellen Messung von Streifen, reduzieren Abfall und sparen Energie. Am wichtigsten ist, dass die Inline-Farbmessung die allgemeine Produktqualität und die Kundenzufriedenheit verbessert. RF
Manfred Binder ist Business Development Director für Inline-Farbmessung bei X-Rite, dem Marktführer für Farbmessung. Er verfügt über 30 Jahre Erfahrung in der Farbmessbranche und ist auf Inline-Anwendungen in der Papier-, Coil-Coating-, Kunststoff-, Textil-, Glas- und Automobilindustrie spezialisiert.