By RF Staff
Rollforming Magazine and all Shield Wall Media titles are changing the format of our Product Features. One purpose of our magazines is to bridge the gap between manufacturers and the end users. This provides more value to both our readers and advertisers. The end users intimately know their challenges and pain points associated with products, processes and equipment. Manufacturers know the material, design and best practices. The new Product Features will draw on both to present solutions to the real-world challenges and concerns facing our readers. Hopefully this will educate the contractors, roll formers and consumers to make better buying decisions and get the most from what they have.
The first Product Feature following this new format is on roll formers.
Item of Concern #1: Gapping changes and adjustment for different types, gauges and hardness of metal
Gapping changes or adjustments are necessary when the material going through the roller dies changes. Roller dies are typically designed to handle a range of materials. Properly adjusted dies are critical for producing a quality panel. Many of the following concerns result from improper adjustment.
Often this can be avoided completely by clearly communicating the types of material you intend to use when initially selecting a roll former. That ensures the different materials will be within the adjustment range for the purchased machine.
The specific profile(s), whether single or multiple pass, thickness and material hardness all affect the required adjustments and need to be communicated to the manufacturer when specifying a machine.
Harder material requires more overbend and generates more spring back. Material thicker than the correct gap setting may impart additional angles into a rib or bend location. Material thinner than the correct gap setting may result in end flare.

Tooling adjustments occur at the overforms. The gap should typically be larger than the gauge of the material processed. If the gap is smaller, it may be an indication that the tooling, bearings or shafts need to be replaced. Some machines have positive stops to prevent the gap from being adjusted to the point the rollers are in contact. This can increase the life of the tooling and decrease the possibility that incorrect adjustments damage the machine.
Frequently adjusting machines allows them to get out of spec. Manufacturers supply gauge blocks allowing the roll former to return their machine to factory zero.
Correct settings, regularly checking the gauge and recalibrating the gap avoids many of the later challenges.
Item of Concern #2: End flare
As with gapping and adjustment issues, end flare is typically addressed best by communicating with your manufacturer when drafting the specifications for your roll former.
End flare can occur on both pre-cut and post-cut machines. Pre-cut lines may experience tooling induced end flare, while post-cut lines may experience shear induced end flare. But, on a good quality, well maintained and properly adjusted mill, end flare should be minimal.
Flare on the lead and tail end of a panel typically occur on pre-cut lines. Post-cut lines form a continuous strip cut after the forming process, preventing flaring. Pre-cut sheets get formed pass, by pass and the panel springs back during the forming process. The extent of flare depends on the profile shape and the yield of the material yield being used.
Flare can also be caused by using material harder than the tooling was designed to form. Overbends in the tooling rolls are not strong enough to account for the higher spring back. Possible solutions are a redesign of roller dies, additional tooling fixtures in the roll former, extending the number of forming stations, a redesign of the over or underlap ribs for better formability and switching to a coil better suited to the process.
Incorrect adjustment or worn mechanical components (tooling, bearings and shafts) result in a loose gap, which also aggravates end flare. A loose gap before an overform pass allows material to form harder and may result in end flare.
Matching gap adjustment to the profile and material type minimizes end flare.
Item of Concern #3: Integration compatibility of roll formers and accessories
Good quality accessories purchased at the same time as the roll former experience few problems with integration.
Decoilers are typically designed as stand alone systems with their own power system (hydraulic or mechanical) for pay-off and mandrel expansion. To integrate a new decoiler with an existing system, you must provide detailed information, including maximum line speed, range of coil width and inner and outer coil diameter. This allows the selection of an appropriate expansion range for the mandrel, cylinder size and lift height and drive train.
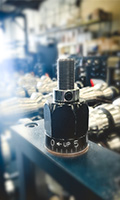
Third-party integration companies provide solutions and support to aid with integration for system components. Their software helps coordinate speed, timing and other critical factors. These third-party systems can increase throughput and be especially helpful when trying to incorporate accessories and mills not specifically designed to work together. They also increase efficiency in matched equipment.
Item of Concern #4: Panels produced not being to specification within acceptable tolerances
Panel tolerances relate to all of the other challenges listed. Gap adjustment, worn tooling, accessories and quality/thickness/hardness of the material all can create issues with panel tolerance.
When the output changes in specification, confirm the coil specifics haven’t changed. Coil is typically slit down from a master coil. Rolls slit from the same master will have the same heat number (batch identification) and should produce consistent results. Coil with a different batch identification may require readjustment to compensate for the changes in coil characteristics.
If the coil has not changed in diameter or hardness, examine the machine. Going through a routine maintenance check list may solve the issue without retooling or calling a technician.
Inconsistency in panels indicates something changed, either the characteristics of the coil or the tooling in the machine.
Conclusion
For manufacturing panels consistency is the obvious key. The most common challenges mentioned by the roll formers we contacted go back to a very few underlying causes.
First and foremost, when you provide specifications to acquire equipment, be detailed and accurate. Discuss options so the machine will meet your needs today and adapt to meet your needs as you grow.
With the right machine, the next step is maintenance and keeping the machine properly adjusted for the quality, type, diameter, and hardness of the coil used.
If confirming the adjustments does not fix a problem, check for worn tooling or integration of peripherals. RF