by AMS Controls
Meet Joe. He has been a folding machine operator at ACME Buildings for over 15 years. ACME Buildings has relied on Joe to run the folding machine and fulfill their trim orders. Joe seems to magically and effortlessly pull off amazing profiles. Joe is fantastic. ACME Buildings has full confidence in Joe. But there is one thing that makes Joe’s manager reach for the bottle of antacid: whenever Joe requests time off.
ACME Buildings is not unique. Countless manufacturers face the same dilemma of not having enough skilled and seasoned folding machine operators. Unfortunately for ACME Buildings, the situation is not getting any better. The 2022 Union Craft Labor Supply Study, conducted by The Association of Union Constructors (TAUC) in conjunction with the Construction Labor Research Council (CLRC), found that there is an increasing shortage of sheet metal workers. This increase has grown from 30% in 2015 to 53% in 2021. Apprenticeship is also suffering, reporting an increase in shortage growing from 29% in 2015 to 40% in 2021. All this shortage spells trouble for ACME Buildings.

Joe’s knowledge of folding machine sequencing is the valuable piece that manufacturers like ACME Buildings are trying to replicate. The situation is compounded further because Joe’s knowledge and expertise is limited to the specific folding machine at ACME Buildings. Since every folding machine has its own unique shape and geometry, the sequence Joe uses at ACME Buildings to bend a profile may not necessarily translate to any other folding machine.
Folding Machine Sequencing Is a Complex Problem
Think of it this way: A simple L-shape profile can be created two ways. Add a bend to the profile, and the number of probable ways to create the profile jumps to eight different possibilities. As more and more bends are added to a profile, the number of probable ways to create a profile grows exponentially. To complicate things for Joe the operator even more, each added bend increases the risk of the profile interfering or colliding with the clamp or other component of the folding machine, which can result in a lot of wasted material, labor and machine time.
Since Joe has years of experience under his belt, Joe has the bend sequence for many commonly used profiles memorized. But as we all know, even with a common profile, there may be customization requested like a longer or shorter segment within the profile, or a different bend radius. These simple requests seem benign, but a small profile change like this is often enough to result in an interference, requiring Joe to rework the bend sequence.
Growing Trend Towards Customization Adds to Complexity
ACME Buildings services an area that has a mix of the old and the new. Their products are used in historical building restorations, older building remodels or additions, and also in the new construction market. ACME Buildings is seeing an increase in the number of custom trim requests. The requests are not just coming from new constructions, but also on the older remodels or restorations as builders seek innovative ways to create solutions for their building problems.
As good as Joe is at his job, it’s impossible and unrealistic for Joe to efficiently sequence all the custom profile requests that will only grow in time. Considering a profile with 18 bends can have as many probable sequences as there are stars in the universe, it’s safe to say that profile sequencing is time consuming, and requires specific expertise.
Relying solely on Joe for their sequencing opens ACME Buildings to some potentially disastrous problems. There will be times when Joe needs time off work: vacations, sick time or family time are all very valid reasons and instances when Joe will be away from his station.
REALITY CHECK #1: By relying heavily on Joe, ACME Buildings had to come to terms with the fact that they will experience job delays stemming from operator availability. In today’s competitive climate, these delays cost ACME Buildings lost opportunities, sales revenue and customer loyalty.

5K gutter profile shown on the Pathfinder Control screen.
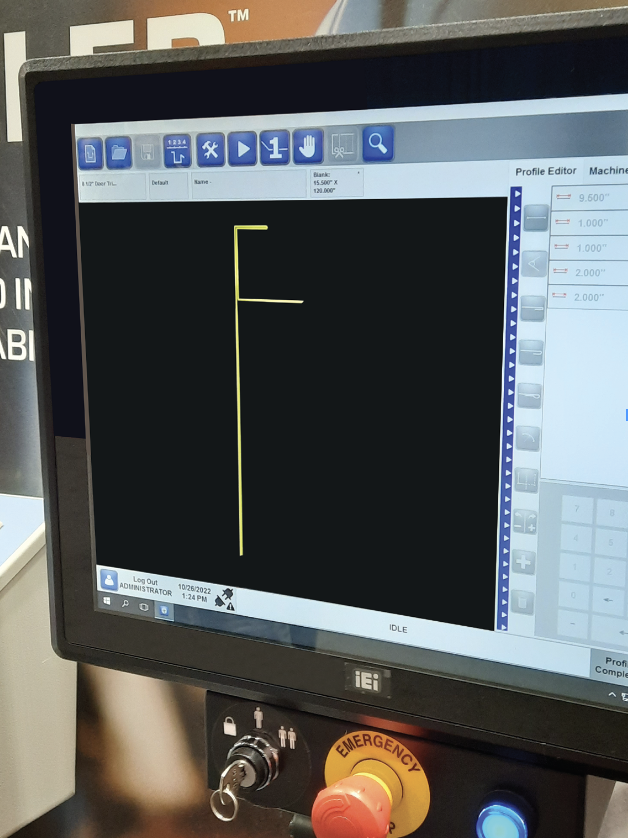
Door trim profile on the Pathfinder Control screen.
Some Sequences Are Better Than Others
As discussed earlier, there may be many sequences that can be used to create a single profile. Some sequences work better than others, while some are just more difficult than they need to be.
Every time a part is handled or manipulated during the folding process, be it a flip, rotate or turn, stress is potentially being placed on the part. We all know some handling is required and unavoidable as part of the folding process. Oftentimes, the stress is minor and does not affect the accuracy of the part.
However, this is not always the case. Minor inaccuracies that happen along the process could stack up and result in a bad dimension within a profile. In short, picking a bad sequence could result in a part that roughly looks like the right part, but the dimensions will not be correct.
REALITY CHECK #2: While custom trim orders are very profitable, any errors and resulting remakes can cause profits to shrink very quickly. The wise move is to ensure trim work is completed accurately and efficiently to maximize profits.
Folding Machine Auto Sequencing Provides Options
Enter folding machine auto sequencing, which can be found on most new folding machines or as retrofit packages for existing folding machines. Auto sequencers use modern day computers and complicated algorithms to analyze the millions of possible sequences for a profile and determine the best sequences. What would normally take a human operator hours to configure can now be generated in mere seconds, all done without the need for any trial and error.
Auto sequencing tools can help identify folding sequences in less time than the conventional way. Equipped with graphic user interfaces and touch screens, these controllers allow operators to simply trace an outline of the profile on the screen with their finger. Novice operators benefit when using auto sequencing capabilities that creates a list of viable sequences based on the profile entered. The operator can then select the sequence that works best for them and follow the step-by-step directions outlined to successfully fabricate a profile. This functionality enables novice operators to gain experience with a folding machine and generate parts all while learning from veteran operators like Joe.
Auto sequencing includes parameters that take into account the unique geometry of each folding machine. These parameters are used to eliminate sequences that can cause an interference. By reducing the opportunity for error, auto sequencing will reduce waste and scrap, reduce guesswork and machine time, and improve efficiency and quality.
A Sustainable Way to Create Reliable Sequences Is Important
Folding machines are revenue generators for manufacturers. It’s therefore important to keep them running as much as possible, and as efficiently as possible.
Ensuring there is a reliable way to develop folding machine sequences when creating profiles will help manufacturers improve efficiency by reducing waste, machine time and improving quality. With a reliable solution for generating sequences that is sustainable and not solely dependent on an experienced folding machine operator, manufacturers will have peace of mind that there will be no disruption in the quality of their product and in their ability to handle any custom profile requests from their customers. RF