Mark Orsborn enjoyed the challenges he faced in his 21 years as owner of Colorado Custom Metal. He found innovative ways to get the panels lifted and stabilized at roof height. For a Harley-Davidson dealership with a curved roof, the crew rolled the 212′-long panels (the longest in his career) in place using ropes drawn through PVC tube to allow the panels to roll into place.
Other unique jobs included a telescope housing on top of Mount Evans, requiring tapered and curved, convex panels on a dome structure.
One of his last big jobs before semi-retiring from the business was the Wings Over the Rockies Air & Space Museum in Denver.
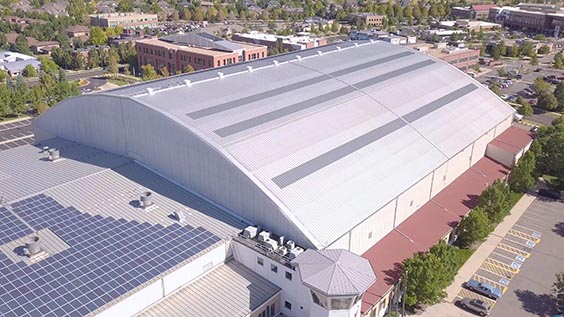
“I was extremely happy when I was chosen as the successful bidder and was asked to work on the flight museum,” Orsborn said. “Having flown hang gliders as an advanced pilot here in Colorado, I have always had a passion for flight.”
The roof was retrofitted with 92,400 square feet of 24-gauge, 18″-wide standing seam Galvalume panel over 6″ of ISO insulation nestled between rows of 16-gauge Galvanized Zee (Z) purlins. It replaced a corrugated metal roof that had been installed in 1938.



Colorado Custom was chosen to retrofit the large radius roof during the cold winter months, while keeping the museum open for its patrons. Increasing the difficulty was the shape and height of the roof—curved and more than 100′ off the ground with a circumference measurement from eave to eave over the top of the barrel at 308 linear feet. The project had to meet the standards of the City and County of Denver’s Historical Landmark Preservation Commission to maintain the same historic look of the building with the new roof.
PROJECT DETAILS: Architect: AH Architecture, Denver Project Consultant: Alec Garbini, Denv Roofing Contractor: Colorado Custom Metal, Glenwood Springs, Colorado Base-Metal Supplier: Fabral Roll Forming: New Tech Machinery, Denver Snow Retention: S-5!, Colorado Springs, Colorado
“That Wings Over the Rockies job was pretty neat,” Orsborn said in hindsight. One of his major problems to solve was how to get the panels up onto the roof without damage. “I was about to build a custom crate to put the new panels in and then raise the crate to the roof a few panels at a time. Then I noticed there were heavy-duty D-rings on the four corners of our New Tech forming machine. I thought what if I just raised the entire machine loaded with coils up to the top of the barrel roof and extruded the roof panels on the large space on top? I consulted with New Tech Manufacturing and they said I could, in fact, do just that. So, we brought in the pros from Winslow Crane Service to handle the lifting of the machine. We did not completely land the weight of the entire machine on the roof in fear of the structure collapsing, so the crane held most of the weight while we ran our panels. It worked beautifully. “
Next, they laid down two layers of 3″ isocyanurate ridged insulation boards nestled tightly between the newly secured Zee purlins. This provided the building with an added R-value of 38.
Finally, installers enclosed the insulation and Zee purlins with a high-temperature ice and water shield membrane. “I used foil-faced insulation boards to allow for strong adhesion of the Ice & Water Shield membrane,” he said.
To cover the 308′-wide barrel roof, Colorado Custom Metal manufactured four separate 77′-long panels and spliced them together. The four panels were attached using a custom expansion joint end lap detail. Workers continued across the roof to hook together subsequent four-panel sections. The panels were curved around the radius of the barrel as each one was installed.
Winslow Crane Service hoisted the roll-forming machine up to the roof level, suspending it a few inches off the roof deck where the roofing panel was manufactured utilizing the 18″ wide 1¾” snap seam profile.
Fabral supplied the 24″-wide, 24-gauge, satin-finished Galvalume roofing coils to make the standing seam panels, as well as more than 300 flat sheets to custom fabricate the flashings, trims, and components for the project.
“We used eight guys [on the job],” Orsborn said, “and that’s a pretty small crew, but it was so easy. Basically, it was just a big square that happened to be curved. I thought I was going to have to put a curving machine up there to shape the panels to meet the roof’s curve, but I laid down a 77′ panel and it laid down so nicely, I didn’t have to curve anything. We just started laying panels.”
PROJECT STATS: • Roof Measurements: Curved roof with a circumference measurement from eave to eave over the top of the barrel @ 308 linear feet • Roof Pitch: 10/12 pitch at the eaves Used 92,400 square feet of 24-gauge, 18"-wide standing seam roofing over 6" of ISO insulation nestled between rows of 16 gauge galvanized Zee Ppurlins • Used S-5! ColorGard snow retention system: -2400 linear feet of unpunched ColorGard -S-5-V Clamps (1600) -VersaClips (1600)
He said he would rather work in cold than heat. “If you’re laying metal down and securing it in place in 0°F weather or 90°F weather, there’s some considerations you have to take. Metal is in a contracted state when it’s super cold, and an expanded state when it’s hot, but you can hardly touch it in the summer; I’d rather do this kind of process in the winter. You can move ice and snow away, but you can’t take heat away.”
It was winter in Denver, so it snowed a lot during the job; not a deterrent for Orsborn’s crew. “We were able to lay the insulation, and ice and water shield from the top going down, which is backward to what you typically do, but all the snow would fall onto our new system then off onto the old, and we would just keep moving.”
He made sure his crew was well-protected. “I would outfit my guys with the latest GORE-TEX gear and goggles and the best gloves and heaters. Thankfully my crews were the tough guys.”
Once the new roof was installed, the project consultant observed heavy snow sliding off the new satin-finished metal roof panels in greater volume than the pre-existing corrugated roof panels.
One of Orsborn’s go-to guys for solving ice and snow avalanche problems was Rob Haddock, owner of S-5!, from nearby Colorado Springs. He had worked with him previously on a $13 million home on Steamboat Mountain. “After 430″ of snow fell that year, it moved the snow fence 3′ over the edge of a copper roof. It was quite a sight to see the snow fence lodged in ice cornice. It was determined that not enough rows of the snow fence product were installed,” said Orsborn. Soon after, Haddock developed an online calculator to help metal roofers like Orsborn determine quickly and easily the correct number of parts required to perform properly as determined by the designated snow loads for any given area.
Noted Orsborn: “I was particularly impressed with S-5! They were the only snow retention company in the marketplace who could tell us the mathematical equation required to calculate the snow loads for their products. There was no guesswork—an engineered avalanche control system with no messy glues or adhesives. We didn’t even have to penetrate the roofing envelope to achieve our desired results. The ColorGard system also provided added strength to the overall diaphragm of the new roof system.” RF